Patty's Industrial Hygiene, Evaluation and Control
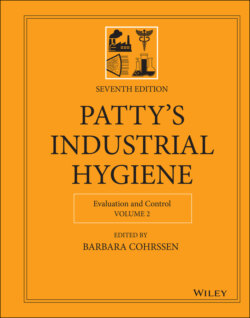
Реклама. ООО «ЛитРес», ИНН: 7719571260.
Оглавление
Группа авторов. Patty's Industrial Hygiene, Evaluation and Control
Table of Contents
List of Tables
List of Illustrations
Guide
Pages
Patty's Industrial Hygiene
Contributors
PREFACE
USEFUL EQUIVALENTS AND CONVERSION FACTORS
BIOLOGICAL MONITORING OF EXPOSURE TO INDUSTRIAL CHEMICALS
1 INTRODUCTION
2 OCCUPATIONAL EXPOSURE ASSESSMENT
2.1 Exposure Monitoring. 2.1.1 Air Sampling
2.1.2 Surface Sampling
2.1.3 Advantages and Limitations of Environmental Monitoring
2.2 Biological Monitoring Approach. 2.2.1 From Exposure to Disease
2.2.2 Biomarkers of Exposure
2.2.3 Biomarkers of Effects
2.2.4 Biomarkers of Individual Susceptibility
3 BIOLOGICAL MONITORING STRATEGY. 3.1 Toxicokinetics
3.1.1 Rate Constant and Half‐Life
3.1.2 Clearance and Volume of Distribution
3.1.3 Saturable Kinetics
3.1.4 Modeling ADME (Absorption, Distribution, Metabolism, and Excretion)
3.2 Sources of Biomonitoring Variability
3.2.1 Biological Variability
3.2.2 Environmental Variability
3.3 Consequences of Variability on the Strategy
3.4 Reference Values for Biological Determinants
3.4.1 History and Concepts of Reference Values
3.4.1.2.1 Germany
3.4.1.2.2 France
3.4.1.2.3 Finland
3.4.2 Quality Control
3.4.3 Ethical Issues
4 BIOLOGICAL MONITORING PRACTICAL APPROACH. 4.1 Common Biological Monitoring Media
4.1.1 Urine
4.1.2 Blood
4.1.3 Exhaled Air
4.1.4 Other Matrices
4.2 Time of Sampling. 4.2.1 Urine
4.2.2 Blood
4.2.3 Exhaled Air
4.3 Criteria for Selection of a Biomarker
4.3.1 Specificity of the Biomarker
4.3.2 Sensitivity and Background Levels
4.3.3 Availability of Analytical Methods
4.3.4 Stability of the Biomarker and Specimen
5 BIOLOGICAL MONITORING FOR METALS AND INORGANIC COMPOUNDS
5.1 Some Examples. 5.1.1 Chromium
5.1.2 Arsenic
5.1.3 Mercury
5.2 Choice of Specimen and Analytical Method
5.3 Factors Interfering with Biological Monitoring of Metals. 5.3.1 Diet and Environment
5.3.2 Other Factors Affecting Biological Levels of Metals
5.4 Current Reference Values for General Population
5.5 Inorganic Gases
5.6 Other Inorganic Pollutants
6 BIOLOGICAL MONITORING OF ORGANIC COMPOUNDS
6.1 Parent Compound
6.2 Eliminated Metabolites
6.3 Deactivation of Electrophilic Metabolites
6.3.1 Glutathione Conjugates
6.4 Adducts with Macromolecules
6.4.1 Adducts with DNA
6.4.2 Adducts with Proteins
6.5 Genetic Polymorphism in Enzyme Activity
7 BIOLOGICAL MONITORING OF EXPOSURES TO MIXTURES
7.1 Toxicodynamic Effects
7.2 Metabolic Interactions
7.2.1 Metabolic Interactions Among Pollutants
7.2.2 Competition for Binding Sites
7.2.3 Effects of Alcohol Consumption
7.2.4 Effect of Medications
8 TRENDS AND CONCLUSIONS
Bibliography
REAL‐TIME ASSESSMENT OF AIR CONTAMINANTS USING VIDEO EXPOSURE MONITORING (VEM) METHODS AND TECHNIQUES
1 INTRODUCTION. 1.1 Historical Development of Real‐Time Assessment of Air Contaminants and Video Exposure Monitoring (VEM)
2 OCCUPATIONAL EXPOSURE. 2.1 Exposure Agents
2.2 Exposure Types
2.3 Exposure Variability
2.4 Exposure Effects
3 DESCRIPTION OF OCCUPATIONAL VIDEO EXPOSURE MONITORING. 3.1 Why Video Exposure Monitoring?
3.2 Assessment Strategy
3.3 Monitoring and Mixed Systems
3.4 Uses
4 SELECTED DIRECT‐READING INSTRUMENTS
4.1 Photoionization Detector
4.2 Aerosol Measurement Instrument
4.3 Response Delay of Direct‐Reading Instruments
5 WIRELESS DATA COMMUNICATIONS. 5.1 Radio Telemetry
5.2 Bluetooth and Wireless Internet Communications
5.3 Internet (Wi‐Fi)
6 VIDEO EQUIPMENT
7 RASPBERRY P – DISRUPTOR INNOVATION FOR VEM
8 MIXING SOFTWARE/INSTRUMENT
8.1 Overlay Technique from NIOSH
8.2 PIMEX – The European Experience
8.3 MVTA – Multimedia Video Task Analysis (University of Wisconsin)
8.4 EVADE – NIOSH Updates Its 1985 Roots in VEM
8.5 Mixing Software Functions
9 DATA INTERPRETATION
9.1 Worker Activities Classification
9.2 Ratio Method
9.3 Regression Functions
10 DISCUSSION. 10.1 Monitoring Subject Selection
10.2 Monitoring Instrument
10.3 Future of the VEM Systems
11 FOUR CASE STUDIES
11.1 Airborne Particulates and Solvents in an Industrial Facility
11.1.1 Purpose
11.1.2 Materials and Methods
11.1.3 Results and Discussion
11.1.4 Conclusions
11.2 Gases – Nitrous Oxide Exposure in a Dental Office Setting
11.2.1 Purpose
11.2.2 Materials and Methods
11.2.3 Results and Discussion
11.2.4 Conclusions
11.3 Radiological – University Laboratory Using Radioactive Materials
11.3.1 Purpose
11.3.2 Materials and Methods
11.3.3 Results and Discussion
11.3.4 Conclusions
11.4 Carbon Dioxide and Heart Rate Monitoring in a Craft Beer Brewing Company
11.4.1 Purpose
11.4.2 Materials and Methods
11.4.3 Results and Discussion
11.4.4 Conclusions
12 SUMMARY
13 FUTURE APPLICATIONS OF VEM
ACKNOWLEDGMENT
Bibliography
COMPUTED TOMOGRAPHY IN INDUSTRIAL HYGIENE
1 INTRODUCTION
1.1 History of Applying Tomography to Environmental Sampling
2 DESIGNING COMPUTED TOMOGRAPHY SYSTEMS
2.1 Test Concentration Maps
2.2 Image Quality Parameters
2.2.1 Nearness
2.2.2 Peak Location Error
2.2.3 Peak Exposure and Peak Height Error
2.2.4 Projection Data Distance
2.2.5 Visual Assessment
3 CT ALGORITHMS FOR THE INDUSTRIAL HYGIENE APPLICATION
3.1 Iterative Methods
3.1.1 Algebraic Reconstruction Techniques (ART)
3.1.2 Maximum Likelihood Expectation Maximization (MLEM) Algorithm
3.1.3 MLEM and Grid Translation
3.1.4 MLEM: Grid Translation‐Multigrid (GT‐MG)
3.2 Smooth Basic Function Minimization (SBFM)
3.3 Non‐iterative Low Third Derivative (LTD) Method
4 SIMULATION STUDIES OF RECONSTRUCTION ALGORITHMS
5 ORS GEOMETRIES FOR CT IMAGING OF CHEMICALS IN AIR
5.1 Simulation Studies of Geometries
5.2 Chamber Studies of Geometries
6 FIELD STUDIES
7 BACKGROUND OPTICAL REMOTE SENSING INSTRUMENTATION
7.1 OP‐FTIR Spectrometer Design
7.2 Theory of Operation
7.3 Quantification
8 CHALLENGES AND FUTURE DIRECTIONS
ACKNOWLEDGMENTS
Bibliography
MATHEMATICAL MODELING OF INDOOR AIR CONTAMINANT CONCENTRATIONS
1 INTRODUCTION
2 CHEMICAL EMISSION RATE FUNCTIONS
2.1 Constant Rates
2.2 A Variable Rate
3 DISPERSION PATTERNS AND WORKER (RECEPTOR) LOCATION
3.1 Well‐Mixed Room
3.2 Near Field/Far Field
3.3 Turbulent Eddy Diffusion
4 SPECIFIC MODELS
4.1 WMR with a Constant Emission Rate
4.2 Well Mixed Room Constant Generation with Backpressure
4.3 WMR with Constant Emission Rate and Local Exhaust Ventilation Removal and Recirculation of Air
4.4 WMR with a Distribution of Particle Sizes
4.5 WMR with an Exponentially Decreasing Emission Rate
4.6 NF/FF with a Constant Emission Rate
4.7 NF/FF with Local Exhaust Removal and Recirculation of Treated Air
4.8 NF/FF with an Exponentially Decreasing Emission Rate
4.9 Hemispherical Turbulent Eddy Diffusion Without Advection and with a Constant Emission Rate
4.10 WMR with a Reversible Sink
5 THE MARKOV CHAIN METHOD. 5.1 Basic Ideas
5.2 Accounting for Ongoing Emission
6 MODELING TURBULENT EDDY DIFFUSION AND ADVECTION
6.1 Modeling Particle Settling
7 IMPLEMENTATION OF MATHEMATICAL MODELS IN MICROSOFT EXCEL
7.1 Stochastic (Monte Carlo Simulation) Approaches
8 MODEL VALIDATION
9 ADDITIONAL MODELS AND RESOURCES
9.1 Primarily European Union Developed Tools
9.2 Selected US EPA Models
9.3 Additional Resources and Information
10 MODEL SELECTION
Bibliography
SENSORS
1 INTRODUCTION
2 PARTICULATE MATTER (PM) SENSORS
2.1 Direct Measures of PM Mass Concentration
2.2 Indirect Measures of PM Mass Concentration
2.2.1 Devices That Incorporate Light Scattering and Gravimetric Elements
2.2.2 Commodity Sensors for Commercial Customers, Researchers, and Hobbyists
2.3 Novel Aerosol Metrics Unrelated to Regulatory Standards
3 GAS SENSORS
3.1 Electrochemical Sensors
3.2 Metal–Oxide–Semiconductor Sensors
3.3 Other Gas Sensing Technologies
4 PHYSICAL AGENTS
4.1 Sound Levels and Noise Exposure
4.2 Temperature
4.3 Vibration
4.4 Radiation
5 APPROACHES FOR SENSOR USE
5.1 Short Duration Sampling and Video Exposure Monitoring
5.2 Personal Exposure Assessment
5.3 Hazard Maps
5.4 Low‐Cost Sensor Networks
6 CONCLUSIONS AND OPPORTUNITIES FOR FUTURE DEVELOPMENTS
References
CHARACTERIZING AIR CONTAMINANT EMISSION SOURCES
1 THE EMISSION INVENTORY
2 ELEMENTS OF THE EMISSION INVENTORY
2.1 Identification of Agents
2.2 Identification of Emission Sites
2.3 Time Factors in Emissions
3 QUANTIFYING EMISSIONS
3.1 Source Sampling
3.2 Materials Balance
3.3 Emission Factors
3.4 Fugitive Sources
4 EMISSION ESTIMATES FROM PLANT AND COMPANY RECORDS AND REPORTS
4.1 Research and Development Records
4.2 Analytical Laboratory Records
4.3 Process and Production Records
4.4 Plant Engineering Records
4.5 Industrial Engineering Records
4.6 Accounting Records
4.7 Personnel Records
4.8 Government‐Mandated Records and Reports
4.9 Record Locations
4.10 Quality of Secondary Data and Records
4.11 Records Retention
5 USE OF THE EMISSION INVENTORY
5.1 Regulatory Requirements
5.2 Determination of Emission Rates
5.3 Workplace Exposure Estimates
5.4 Case Study: Sample Calculations Demonstrating the Use of an Emission Inventory and Characterization
Bibliography
ENGINEERING CONTROL OF AIRBORNE CONTAMINANTS: HISTORY, PHILOSOPHY, AND THE DEVELOPMENT OF PRIMARY APPROACHES
1 INTRODUCTION
2 ENGINEERING CONTROL TYPES
2.1 Substitution and Elimination
2.2 Isolation and Enclosure
2.3 Scope and Other Issues
3 ENGINEERING CONTROL STRATEGIES
3.1 Control of Toxic Materials
3.1.1 Eliminate the Toxic Material
3.1.2 Replace with Alternative Material: Substitution
3.1.2.1 HISTORICAL TOXIC CHEMICALS USE REDUCTION AND REPLACEMENT APPROACHES
3.1.2.2 STATE TOXIC USE REDUCTION PROGRAMS
3.1.2.3 INDUSTRY‐BASED PROGRAMS
3.1.2.4 OUTCOME OF REPLACEMENT TECHNOLOGY
3.1.3 Dust Control
3.1.3.1 MOISTURE CONTENT OF MATERIAL
3.1.3.2 PARTICLE SIZE
3.1.3.3 DUST CONTROLLED FORMS
3.1.3.4 SLURRY FORM
3.1.4 Impurities in Production Chemicals
3.1.4.1 RESIDUAL MONOMER IN POLYMER
3.1.4.2 SOLVENT IMPURITIES
3.2 Equipment and Processes
3.2.1 Diagnostic Air Sampling
3.2.2 Equipment. 3.2.2.1 ANCILLARY EQUIPMENT
3.2.2.2 MAJOR PROCESSING EQUIPMENT
3.2.3 Processes
3.3 Work Task Modification, Automation, and Robotics
3.4 Facility Layout and Equipment Placement
3.4.1 Material Transport
3.4.2 General Considerations
3.4.3 Workstations
3.4.4 Service and Maintenance
3.4.5 Segregation of Operation
3.4.6 Isolation of the Worker
3.5 Ventilation
4 STANDARDS AND GUIDELINES
Bibliography
INDUSTRIAL VENTILATION
1 INTRODUCTION
2 FUNDAMENTAL DEFINITIONS AND PHYSICAL RELATIONSHIPS
2.1 Airflow Rate
2.2 Density Correction for Air at Non‐STP
2.3 Velocity Pressure and Velocity
2.4 Static Pressure (SP)
2.5 Total Pressure
2.6 Static Pressure (Energy) Losses
3 LOCAL EXHAUST VENTILATION
3.1 Individual Components of an LEV System. 3.1.1 Hoods
3.1.2 Ductwork
3.1.3 Air Cleaners
3.1.4 Fans
3.1.5 Stacks
3.2 LEV Hood Types
3.2.1 Enclosure Hoods
3.2.2 Booth‐Type Hoods
3.2.3 Capture or Exterior Hoods
3.2.4 Receiving Hoods
3.3 Factors Influencing the Performance of LEV Systems
3.3.1 Capture/Control Velocities
3.3.2 Airflow Characteristics at a Capture Hood
3.3.3 Determining Airflow Rates into Hoods Using Q = VA
3.3.4 Hood‐Related Equations
3.3.5 Effects of Flanging
3.3.6 Air Distribution in the Face of Enclosing Hoods
3.3.7 Enclosure of the Emission Source
3.3.8 Capture of Contaminants
3.3.9 Keeping Contaminants Out of Breathing Zone
3.3.10 Providing Makeup Air
3.3.11 Low Volume High Velocity Exhaust Systems
3.3.12 Duct Velocities
4 FACTORS INFLUENCING THE DESIGN OF NEW LEV SYSTEMS
4.1 Ventilation Regulations and Standards. 4.1.1 OSHA Codes
4.2 ANSI Z9 Standards
5 DILUTION VENTILATION
5.1 Natural Ventilation
5.2 Mechanically Controlled Ventilation
5.3 Dilution Ventilation for Contaminant Control
5.4 Estimating Dilution Ventilation Volume Flow Rates
5.5 Dilution Ventilation Airflow Patterns
5.5.1 Air Inlets
5.5.2 Air Exhausts and Outlets
5.6 Which is More Appropriate, LEV or Dilution Ventilation as a Primary Control?
6 TESTING AND MONITORING. 6.1 Acceptance and Start‐Up Testing
6.2 Checking Preconstruction Details
6.3 Airflow
6.4 Performance
6.4.1 Qualitative Methods
6.4.2 Semiquantitative
6.4.3 Quantitative
6.5 Periodic Maintenance Testing
7 MAKEUP AIR AND RECIRCULATION OF EXHAUST AIR
7.1 Need for Adequate Makeup Air
7.2 Principles of Supplying Air
7.3 Recirculation of Exhaust Air
7.3.1 Circumstances Permitting Recirculation of Air
7.4 Additional Design Safeguards for Recirculated Air
References
Further Reading
RESPIRATORY PROTECTIVE EQUIPMENT
1 HISTORICAL REVIEW
2 RESPIRATOR PERFORMANCE
2.1 Laboratory Tests
2.2 Workplace Testing
3 RESPIRATOR CLASSIFICATION
3.1 Positive Pressure Classification
3.2 Air‐Purifying Respirators
3.2.1 Particulate Respirators
3.2.1.1 FILTER CLASSIFICATION
3.2.2 Gas and Vapor Respirators
3.2.2.1 CHEMICAL CARTRIDGE RESPIRATORS
3.2.2.2 GAS MASKS
3.2.2.3 GAS AND VAPOR CARTRIDGES AND CANISTERS
3.2.2.4 COMBINATION CARTRIDGES AND CANISTERS
3.2.2.5 CARBON MONOXIDE
3.2.3 Powered Air‐Purifying Respirators
3.3 Atmosphere‐Supplying Respirators. 3.3.1 Self‐Contained Breathing Apparatus
3.3.1.1 OPEN‐CIRCUIT SELF‐CONTAINED BREATHING APPARATUS
3.3.1.2 CLOSED‐CIRCUIT SELF‐CONTAINED BREATHING APPARATUS AND CLOSED‐CIRCUIT ESCAPE RESPIRATORS (CCERS)
3.3.2 Supplied‐Air Respirators
3.3.2.1 TYPE C SARS
3.4 Chemical, Biological, Radioactive, Nuclear (CBRN) Approval
3.5 Supplied‐Air Suits
3.6 Escape Respirators
4 RESPIRATOR SELECTION AND USE
4.1 Respiratory Hazards
4.1.1 Oxygen Deficiency
4.1.2 Biological Agents
4.1.3 Engineered Nanoparticles
4.2 Respirator Program
4.2.1 Program Administration
4.2.2 Respirator Selection
4.2.3 Medical Evaluation
4.2.4 Fit Testing
4.2.5 Qualitative Fit Tests
4.2.6 Quantitative Fit Testing
4.2.7 Minimum Fit Requirements
4.2.8 Training
4.2.9 Evaluation of Respirator Program Effectiveness
4.2.10 Maintenance and Care of RPE
4.2.11 Breathing Air Quality
4.3 Special Problems with Selecting and Using Respirators. 4.3.1 Respirators and Hair
4.3.2 Cold Temperatures
4.3.3 Corrective Lenses
4.3.4 Communications
ACKNOWLEDGMENTS
Bibliography
CHEMICAL PROTECTIVE CLOTHING
1 INTRODUCTION
1.1 How to Select the Most Appropriate Chemical Protective Clothing
1.1.1 Permeation, Penetration, and Degradation
1.1.2 The Selection Process
1.1.3 Eleven Important Considerations for the Selection and Use of Chemical Protective Clothing
2 BARRIERS USED IN CHEMICAL PROTECTIVE CLOTHING
3 CHEMICALS USED FOR EVALUATING CHEMICAL PROTECTIVE CLOTHING. 3.1 ASTM F1001 Standard Guide
3.2 Selection Recommendations
4 CLASSIFICATION FOR CHEMICALS. 4.1 ASTM F1186 Standard Classification System for Chemicals According to Functional Groups
5 STANDARDS FOR CHEMICAL PROTECTIVE CLOTHING
5.1 ASTM Standards (www.astm.org)
5.2 NFPA Standards (www.nfpa.org)
5.3 EN‐ISO Standards (www.cen.eu and www.iso.org)
GLOSSARY
CONTROL BANDING: BACKGROUND, EVOLUTION, AND APPLICATION
1 INTRODUCTION
1.1 Brief Description of CB
1.2 Terminology
1.3 Scope and Objectives
2 PART I: ESTABLISHING THE BASIS FOR CONTROL BANDING APPROACHES. 2.1 Challenges to the Traditional OEL Approach
2.2 The UK Experience: Response to COSHH Regulations
2.3 The Global Experience: What About the Others?
3 PART II: HISTORY AND EVOLUTION OF CONTROL BANDING. 3.1 The Origins of CB
3.2 Simple Measures of Toxicity
3.3 Occupational Exposure Bandings
3.4 Linking Toxicological Data with Appropriate Levels of Control
3.5 Hazard + Exposure → Risk → Control Strategy
3.6 The COSHH Essentials Strategy
3.6.1 Basic Concepts
3.6.2 Toxicological Considerations
3.6.3 IH Considerations
3.6.4 Providing Control Guidance to Users
4 PART III: VALIDATION AND VERIFICATION OF CB STRATEGIES
4.1 Exposure Monitoring
4.2 Validation Studies
5 PART IV: CB EVALUATION AND THE INTERNATIONAL EXPERIENCE. 5.1 The International Paradox for Simplified Solutions to Reduce Risk
5.2 International Validation and Growth from the COSHH Essentials
5.3 The Reach of REACH
5.4 CB as a Gold Standard; The Nanomaterial Challenge
6 PART V: PRACTICAL EXAMPLES OF CB APPLICATION FOR THE NEW IH
An All Too Familiar Scenario
6.1 Limited Time, Resources, and OEL Guidance
6.1.1 An IH World Without OELs
6.1.2 A World of Generalists
6.1.3 Developed and Still Developing Countries Approaching Parity?
6.2 Control Banding and the Newer IH's Toolbox
6.2.1 Occupational Exposure Banding
6.2.2 Control Banding Tools – Bulk Chemicals and Beyond
6.2.3 Control Banding Tools – Moving Away from IH
6.2.4 Control Banding Acceptance by National Organizations
6.3 Control Banding – Multidisciplinary EHS Applications
6.4 Control Banding – See Workplaces Through a Professional's Eyes
Control Banding, the New IH, and The All Too Familiar Scenario
7 PART VI: DISCUSSION
7.1 CB and the State of the IH Profession
7.2 Lessons Learned from CB in Practice
8 PART VII: SUMMARY, CONCLUSIONS, AND RECOMMENDATIONS
ACKNOWLEDGMENTS
Bibliography
OCCUPATIONAL SAFETY AND HEALTH LAW
1 INTRODUCTION TO THE FEDERAL OCCUPATIONAL SAFETY AND HEALTH ACT
1.1 Entities Responsible for Implementing the OSH Act
1.2 Scope of OSH Act's Coverage
2 OCCUPATIONAL SAFETY AND HEALTH STANDARDS DEVELOPMENT
2.1 Types of Standards. 2.1.1 Consensus Standards
2.1.2 Emergency Temporary Standards
2.1.3 Permanent Standards
2.2 Requirements for Standards Adoption
2.2.1 Significant Risk
2.2.2 Economic and Technological Feasibility
2.2.3 Rulemaking Analysis Requirements
2.2.3.1 NATIONAL ENVIRONMENTAL POLICY ACT
2.2.3.2 REGULATORY FLEXIBILITY ACT AND THE SMALL BUSINESS REGULATORY ENFORCEMENT AND FAIRNESS ACT
2.2.3.3 PAPERWORK REDUCTION ACT
2.2.3.4 EXECUTIVE ORDERS
2.2.3.5 INFORMATION QUALITY ACT
3 EMPLOYER DUTIES UNDER THE OSH ACT
3.1 The General Duty Clause
3.1.1 Condition or Activity Must Be a “Recognized” Hazard
3.1.2 Hazard Must Be Causing or Likely to Cause Death or Serious Physical Injury
3.1.3 Feasible Abatement Method
3.2 Employer Duties Arising from Single‐Substance Health Standards
3.2.1 Acrylonitrile
3.2.2 Asbestos
3.2.3 Benzene
3.2.4 Beryllium
3.2.5 1,3‐Butadiene
3.2.6 Cadmium
3.2.7 Cotton Dust
3.2.8 1,2‐Dibromo‐3‐Chloropropane
3.2.9 Ethylene Oxide
3.2.10 Formaldehyde
3.2.11 Hexavalent Chromium
3.2.12 Inorganic Arsenic
3.2.13 Lead
3.2.14 Methylene Chloride
3.2.15 Methylenedianiline
3.2.16 Noise
3.2.17 Respirable Crystalline Silica
3.2.18 Vinyl Chloride
3.3 Employer Duties Arising from Generic Health Standards. 3.3.1 Bloodborne Pathogens
3.3.2 Carcinogens
3.3.3 Coke Oven Emissions
3.3.4 Hazard Communication
3.3.5 Hazardous Waste Operations
3.3.6 Respiratory Protection
3.4 Employer Duties Arising from Selected Safety Standards. 3.4.1 Confined Spaces
3.4.2 Personal Protective Equipment
3.5 Other Standards Not Promulgated by OSHA or Nullified by Congress
3.5.1 Combustible Dust
3.5.2 Diacetyl
3.5.3 Ergonomics
3.5.4 Indoor Air Quality
3.5.5 Tuberculosis and other Infectious Diseases
3.5.6 Workplace Violence Prevention
3.6 Employer Duties Arising from Specific Regulations. 3.6.1 Recordkeeping
3.6.2 Reporting Occupational Injuries and Illnesses to OSHA
3.6.3 Access to Employee Exposure and Medical Records
4 CHALLENGING A STANDARD AFTER PROMULGATION. 4.1 Judicial Review
4.2 Variance from Compliance with Specific Standards. 4.2.1 Permanent Variance
4.2.2 Temporary Variance
4.2.3 Experimental Variance
4.2.4 National Defense Variance
5 ENFORCEMENT OF THE OSH ACT
5.1 Types of Inspections
5.2 Right to Inspect and Warrants
5.2.1 Probable Cause Necessary for Warrant
5.2.2 Ex Parte Warrants
5.2.3 Challenging the Validity of a Warrant
5.3 Inspection Procedures
5.4 Imminent Danger Inspections
5.5 Types of Violations
5.5.1 DeMinimis Violations
5.5.2 Other‐than‐Serious Violations
5.5.3 Serious Violations
5.5.4 Willful Violations
5.5.5 Repeated Violations
5.5.6 Failure‐to‐Abate Violations
5.6 Civil Penalties
5.7 Criminal Sanctions
5.8 Specific Enforcement Policies. 5.8.1 Cases Subject to Violation‐by‐Violation Penalties
5.8.2 Multi‐Employer Citation Policy
6 CONTESTATION PROCEEDINGS. 6.1 Contesting Citations and Penalties
6.2 Employer's Affirmative Defenses
6.3 Courts of Appeals Review
7 RIGHTS OF EMPLOYEES AND THEIR REPRESENTATIVES UNDER THE OSH ACT. 7.1 Information Rights. 7.1.1 Poster
7.1.2 Injury and Illness Log
7.2 Right to Refuse Hazardous Work under Section 11(c) of the OSH Act
7.3 Right to Request and Participate in a Compliance Inspection
7.4 Rights to Participate in Litigation before the Review Commission
7.5 Right to be Notified of Possible Imminent Danger and Right to Seek Relief for Imminent Dangers
7.6 Right to File a Complaint against State Program Administration
7.7 Right to Access Exposure Records
7.8 Antidiscrimination Rights
8 VOLUNTARY COMPLIANCE PROGRAMS. 8.1 On‐Site Consultation Program
8.1.1 Safety and Health Achievement Recognition Program (SHARP)
8.2 OSHA's Cooperative Programs. 8.2.1 Alliance Program
8.2.2 OSHA Strategic Partnership Program
8.2.3 Voluntary Protection Program
8.2.4 OSHA Challenge Program
9 REGULATION OF OCCUPATIONAL SAFETY AND HEALTH BY THE STATES
10 REGULATION OF OCCUPATIONAL SAFETY AND HEALTH BY OTHER FEDERAL STATUTES. 10.1 Partial Exemption from Coverage by the OSH Act
10.2 Selected Other Federal Agencies Affecting Occupational Safety and Health. 10.2.1 Mine Safety and Health Administration
10.2.2 U.S. Chemical Safety and Hazard Investigation Board
10.2.3 Nuclear Regulatory Commission
10.2.4 Consumer Product Safety Commission
10.2.5 Environmental Protection Agency
10.2.6 Department of Transportation
11 FUTURE OF OCCUPATIONAL SAFETY AND HEALTH LAW
ENDNOTES
Bibliography
Index
WILEY END USER LICENSE AGREEMENT
Отрывок из книги
Seventh Edition
Volume 2
.....
1 foot of water pressure = 0.4335 pound per square inch
1 inch of mercury pressure = 0.4912 pound per square inch
.....