Welding Metallurgy
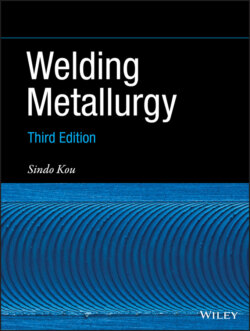
Реклама. ООО «ЛитРес», ИНН: 7719571260.
Оглавление
Sindo Kou. Welding Metallurgy
Table of Contents
List of Tables
List of Illustrations
Guide
Pages
Welding Metallurgy
Copyright
Preface to Third Edition
1 Welding Processes
1.1 Overview. 1.1.1 Fusion Welding Processes
1.1.1.1 Power Density of Heat Source
1.1.1.2 Welding Processes and Materials
1.1.1.3 Types of Joints and Welding Positions
1.1.2 Solid‐State Welding Processes
1.2 Gas Welding. 1.2.1 The Process
1.2.2 Three Types of Flames. 1.2.2.1 Neutral Flame
1.2.2.2 Reducing Flame
1.2.2.3 Oxidizing Flame
1.2.3 Advantages and Disadvantages
1.3 Arc Welding. 1.3.1 Shielded Metal Arc Welding
1.3.1.1 Functions of Electrode Covering
1.3.1.2 Advantages and Disadvantages
1.3.2 Gas–Tungsten Arc Welding. 1.3.2.1 The Process
1.3.2.2 Polarity
1.3.2.3 Electrodes
1.3.2.4 Shielding Gases
1.3.2.5 Advantages and Disadvantages
1.3.3 Plasma Arc Welding. 1.3.3.1 The Process
1.3.3.2 Arc Initiation
1.3.3.3 Keyholing
1.3.3.4 Advantages and Disadvantages
1.3.4 Gas–Metal Arc Welding. 1.3.4.1 The Process
1.3.4.2 Shielding Gases
1.3.4.3 Modes of Metal Transfer
1.3.4.4 Advantages and Disadvantages
1.3.5 Flux‐Cored Arc Welding. 1.3.5.1 The Process
1.3.6 Submerged Arc Welding. 1.3.6.1 The Process
1.3.6.2 Advantages and Disadvantages
1.3.7 Electroslag Welding. 1.3.7.1 The Process
1.3.7.2 Advantages and Disadvantages
1.4 High‐Energy‐Beam Welding. 1.4.1 Electron Beam Welding. 1.4.1.1 The Process
1.4.1.2 Advantages and Disadvantages
1.4.2 Laser Beam Welding. 1.4.2.1 The Process
1.4.2.2 Reflectivity
1.4.2.3 Shielding Gas
1.4.2.4 Laser‐Assisted Arc Welding
1.4.2.5 Advantages and Disadvantages
1.5 Resistance Spot Welding
1.6 Solid‐State Welding. 1.6.1 Friction Stir Welding
1.6.2 Friction Welding
1.6.3 Explosion and Magnetic‐Pulse Welding
1.6.4 Diffusion Welding
Examples
Answer:
Answer
References
Further Reading
Problems
2 Heat Flow in Welding
2.1 Heat Source. 2.1.1 Heat Source Efficiency
2.1.1.1 Definition
2.1.1.2 Measurements
2.1.1.3 Heat Source Efficiencies in Various Welding Processes
2.1.2 Melting Efficiency
2.1.3 Power Density Distribution of Heat Source. 2.1.3.1 Effect of Electrode Tip Angle
2.1.3.2 Measurements
2.2 Heat Flow During Welding. 2.2.1 Response of Material to Welding Heat Source
2.2.2 Rosenthal's Equations
2.2.2.1 Rosenthal's Two‐Dimensional Equation
2.2.2.2 Rosenthal's Three‐Dimensional Equation
2.2.2.3 Step‐by‐Step Application of Rosenthal's Equations
2.2.3 Adams' Equations
2.3 Effect of Welding Conditions
2.4 Computer Simulation
2.5 Weld Thermal Simulator. 2.5.1 The Equipment
2.5.2 Applications
2.5.3 Limitations
Examples
Answer:
Answer:
Answer:
References
Further Reading
Problems
3 Fluid Flow in Welding
3.1 Fluid Flow in Arcs
3.1.1 Sharp Electrode
3.1.2 Flat‐End Electrode
3.2 Effect of Metal Vapor on Arcs. 3.2.1 Gas−Tungsten Arc Welding
3.2.2 Gas−Metal Arc Welding
3.3 Arc Power‐ and Current‐Density Distributions
3.4 Fluid Flow in Weld Pools. 3.4.1 Driving Forces for Fluid Flow
3.4.2 Heiple's Theory for Weld Pool Convection
3.4.3 Physical Simulation of Fluid Flow and Weld Penetration
3.4.4 Computer Simulation of Fluid Flow and Weld Penetration
3.5 Flow Oscillation and Ripple Formation
3.6 Active Flux GTAW
3.7 Resistance Spot Welding
Examples
Answer
Answer
References
Further Reading
Problems
4 Mass and Filler–Metal Transfer
4.1 Convective Mass Transfer in Weld Pools
4.2 Evaporation of Volatile Solutes
4.3 Filler‐Metal Drop Explosion and Spatter
4.4 Spatter in GMAW of Magnesium
4.5 Diffusion Bonding
Examples
Answer:
Answer:
References
Problems
5 Chemical Reactions in Welding
5.1 Overview. 5.1.1 Effect of Nitrogen, Oxygen, and Hydrogen
5.1.2 Protection Against Air
5.1.3 Evaluation of Weld Metal Properties
5.2 Gas–Metal Reactions
5.2.1 Thermodynamics of Reactions
5.2.2 Hydrogen. 5.2.2.1 Magnesium
5.2.2.2 Aluminum
5.2.2.3 Titanium
5.2.2.4 Copper
5.2.2.5 Steels
Sources of Hydrogen
Measuring Hydrogen Content
Hydrogen Reduction Methods
5.2.3 Nitrogen
5.2.3.1 Steel
Effect of Nitrogen
Protection Against Nitrogen
5.2.3.2 Titanium
5.2.4 Oxygen. 5.2.4.1 Magnesium
5.2.4.2 Aluminum
5.2.4.3 Titanium
5.2.4.4 Steel. Sources of Oxygen
Effect of Oxygen
5.3 Slag–Metal Reactions. 5.3.1 Thermochemical Reactions
5.3.1.1 Decomposition of Flux
5.3.1.2 Removal of S and P from Liquid Steel
5.3.2 Effect of Flux on Weld Metal Oxygen
5.3.3 Types of Fluxes, Basicity Index, and Weld Metal Properties
5.3.4 Basicity Index
5.3.5 Electrochemical Reactions
Examples
Answer:
Answer:
References
Further Reading
Problems
6 Residual Stresses, Distortion, and Fatigue
6.1 Residual Stresses
6.1.1 Development of Residual Stresses. 6.1.1.1 Stresses Induced By Welding
6.1.1.2 Welding
6.1.2 Analysis of Residual Stresses
6.2 Distortion. 6.2.1 Cause
6.2.2 Remedies
6.3 Fatigue. 6.3.1 Mechanism
6.3.2 Fractography
6.3.3 S–N Curves
6.3.4 Effect of Joint Geometry
6.3.5 Effect of Stress Raisers
6.3.6 Effect of Corrosion
6.3.7 Remedies. 6.3.7.1 Shot Peening
6.3.7.2 Reducing Stress Raisers
6.3.7.3 Laser Shock Peening
6.3.7.4 Use of Low–Transformation–Temperature Fillers
Examples
Answer:
Answer:
References
Further Reading
Problems
7 Introduction to Solidification
7.1 Solute Redistribution During Solidification. 7.1.1 Directional Solidification
7.1.2 Equilibrium Segregation Coefficient k
7.1.3 Four Cases of Solute Redistribution
7.2 Constitutional Supercooling
7.3 Solidification Modes
7.4 Microsegregation Caused by Solute Redistribution
7.5 Secondary Dendrite Arm Spacing
7.6 Effect of Dendrite Tip Undercooling
7.7 Effect of Growth Rate
7.8 Solidification of Ternary Alloys. 7.8.1 Liquidus Projection
7.8.2 Solidification Path
7.8.3 Ternary Magnesium Alloys
7.8.4 Ternary Fe‐Cr‐Ni Alloys
7.8.4.1 Fe‐Cr‐Ni Phase Diagram
7.8.4.2 Solidification Paths
7.8.4.3 Microstructure. Primary Austenite
Primary Ferrite
Examples
Answer
Answer
References
Further Reading
Problems
8 Solidification Modes
8.1 Solidification Modes
8.1.1 Temperature Gradient and Growth Rate
8.1.2 Variations in Solidification Mode Across Weld
8.2 Dendrite Spacing and Cell Spacing
8.3 Effect of Welding Parameters. 8.3.1 Solidification Mode
8.3.2 Dendrite and Cell Spacing
8.4 Refining Microstructure Within Grains
8.4.1 Arc Oscillation
8.4.2 Arc Pulsation
Examples
Answer
Answer
References
Further Reading
Problems
9 Nucleation and Growth of Grains
9.1 Epitaxial Growth at the Fusion Line
9.2 Nonepitaxial Growth at the Fusion Line. 9.2.1 Mismatching Crystal Structures
9.2.2 Nondendritic Equiaxed Grains
9.3 Growth of Columnar Grains
9.4 Effect of Welding Parameters on Columnar Grains
9.5 Control of Columnar Grains
9.6 Nucleation Mechanisms of Equiaxed Grains. 9.6.1 Microstructure Around Pool Boundary
9.6.2 Dendrite Fragmentation
9.6.3 Grain Detachment
9.6.4 Heterogeneous Nucleation
9.6.5 Effect of Welding Parameters on Heterogeneous Nucleation
9.6.6 Surface Nucleation
9.7 Grain Refining
9.7.1 Inoculation
9.7.2 Weld Pool Stirring. 9.7.2.1 Magnetic Weld Pool Stirring
9.7.2.2 Ultrasonic Weld Pool Stirring
9.7.3 Arc Pulsation
9.7.4 Arc Oscillation
9.8 Identifying Grain‐Refining Mechanisms. 9.8.1 Overlap Welding Procedure
9.8.2 Identifying the Grain‐Refining Mechanism
9.8.3 Effect of Arc Oscillation on Dendrite Fragmentation
9.8.4 Effect of Arc Oscillation on Constitutional Supercooling
9.8.5 Effect of Composition on Grain Refining by Arc Oscillation
9.9 Grain‐Boundary Migration
Examples
Answer:
Answer:
References
Further Reading
Problems
10 Microsegregation
10.1 Microsegregation in Welds
10.2 Effect of Travel Speed on Microsegregation
10.3 Effect of Primary Solidification Phase on Microsegregation
10.4 Effect of Maximum Solid Solubility on Microsegregation
Examples
Answer:
Answer:
References
Further Reading
Problems
11 Macrosegregation
11.1 Macrosegregation in the Fusion Zone
11.2 Quick Freezing of One Liquid Metal in Another
11.3 Macrosegregation in Dissimilar‐Filler Welding. 11.3.1 Bulk Weld‐Metal Composition
11.3.2 Mechanism I
11.3.3 Mechanism II
11.4 Macrosegregation in Dissimilar‐Metal Welding. 11.4.1 Mechanism I
11.4.2 Mechanism II
11.5 Reduction of Macrosegregation
11.6 Macrosegregation in Multiple‐Pass Welds
Answer:
References
Further Reading
Problems
12 Some Alloy‐Specific Microstructures and Properties
12.1 Austenitic Stainless Steels. 12.1.1 Microstructure Evolution in Stainless Steels
12.1.2 Mechanisms of Ferrite Formation
12.1.3 Prediction of Ferrite Content
12.1.4 Effect of Cooling Rate. 12.1.4.1 Changes in Solidification Mode
12.1.4.2 Dendrite Tip Undercooling
12.2 Low‐Carbon, Low‐Alloy Steels. 12.2.1 Microstructure Development
12.2.2 Factors Affecting Microstructure
12.2.3 Weld Metal Toughness
12.3 Ultralow Carbon Bainitic Steels
12.4 Creep‐Resistant Steels
12.5 Hardfacing of Steels
References
Further Reading
Problems
13 Solidification Cracking
13.1 Characteristics of Solidification Cracking
13.2 Theories of Solidification Cracking
13.2.1 Criterion for Cracking Proposed by Kou
13.2.2 Index for Crack Susceptibility Proposed by Kou
13.2.3 Previous Theories
13.3 Binary Alloys and Analytical Equations
13.4 Solidification Cracking Tests
13.4.1 Varestraint Test
13.4.2 Controlled Tensile Weldability Test
13.4.3 Transverse‐Motion Weldability Test
13.4.4 Circular‐Patch Test
13.4.5 Houldcroft Test
13.4.6 Cast‐Pin Test
13.4.7 Ring‐Casting Test
13.4.8 Other Tests
13.5 Solidification Cracking of Stainless Steels. 13.5.1 Primary Solidification Phase
13.5.2 Mechanism of Crack Resistance
13.6 Factors Affecting Solidification Cracking. 13.6.1 Primary Solidification Phase
13.6.2 Grain Size
13.6.3 Solidification Temperature Range
13.6.4 Back Diffusion
13.6.5 Dihedral Angle
13.6.6 Grain‐Boundary Angle
13.6.7 Degree of Restraint
13.7 Reducing Solidification Cracking. 13.7.1 Control of Weld Metal Composition
13.7.2 Control of Weld Microstructure
13.7.3 Control of Welding Conditions
13.7.4 Control of Weld Shape
Examples
References
Further Reading
Problems
14 Ductility‐Dip Cracking
14.1 Characteristics of Ductility‐Dip Cracking
14.2 Theories of Ductility‐Dip Cracking
14.3 Test Methods
14.4 Ductility‐Dip Cracking of Ni‐Base Alloys. 14.4.1 Grain‐Boundary Sliding
14.4.2 Grain‐Boundary Misorientation
14.4.3 Grain‐Boundary Tortuosity and Precipitates
14.4.4 Grain Size
14.4.5 Factors Affecting Ductility‐Dip Cracking
14.5 Ductility‐Dip Cracking of Stainless Steels
Examples
References
Further Reading
Problems
15 Liquation in the Partially Melted Zone
15.1 Formation of the Partially Melted Zone
15.2 Liquation Mechanisms
15.2.1 Mechanism I: Alloy with Co>CSM
15.2.2 Mechanism II: Alloy with Co<CSM and no AxBy or Eutectic
15.2.3 Mechanism III: Alloy with Co<CSM and AxBy or Eutectic
15.2.4 Additional Mechanisms of Liquation
15.3 Directional Solidification of Liquated Material
15.4 Grain‐Boundary Segregation
15.5 Loss of Strength and Ductility
15.6 Hydrogen Cracking
15.7 Effect of Heat Input
15.8 Effect of Arc Oscillation
Examples
References
Problems
16 Liquation Cracking
16.1 Liquation Cracking in Arc Welding
16.1.1 Crack Susceptibility Tests
16.1.1.1 Varestraint Testing
16.1.1.2 Circular‐Patch Testing
16.1.1.3 Hot Ductility Testing
16.1.2 Mechanism of Liquation Cracking
16.1.3 Predicting Effect of Filler Metal on Crack Susceptibility
16.1.4 Factors Affecting Liquation Cracking. 16.1.4.1 Filler Metal
16.1.4.2 Heat Source
16.1.4.3 Degree of Restraint
16.1.4.4 Base Metal
16.2 Liquation Cracking in Resistance Spot Welding
16.3 Liquation Cracking in Friction Stir Welding
16.4 Liquation Cracking in Dissimilar‐Metal FSW
Examples
References
Problems
17 Introduction to Solid‐State Transformations
17.1 Work‐Hardened Materials
17.2 Heat‐Treatable Al Alloys
17.3 Heat‐Treatable Ni‐Base Alloys
17.4 Steels. 17.4.1 Fe‐C Phase Diagram and CCT Diagrams
17.4.2 Carbon Steels
17.4.3 Dual‐Phase Steels
17.5 Stainless Steels. 17.5.1 Types of Stainless Steels
17.5.2 Sensitization of Unstabilized Grades
17.5.3 Sensitization of Stabilized Grades
17.5.4 σ‐Phase Embrittlement
Examples
References
Problems
18 Heat‐Affected‐Zone Degradation of Mechanical Properties
18.1 Grain Coarsening
18.2 Recrystallization and Grain Growth
18.3 Overaging in Al Alloys. 18.3.1 Al‐Cu‐Mg (2000‐Series) Alloys. 18.3.1.1 Microstructure and Strength
18.3.1.2 Effect of Welding Parameters or Process
18.3.2 Al‐Mg‐Si (6000‐Series) Alloys. 18.3.2.1 Microstructure and Strength
18.3.2.2 Effect of Welding Processes and Parameters
18.3.3 Al‐Zn‐Mg (7000‐Series) Alloys
18.4 Dissolution of Precipitates in Ni‐Base Alloys
18.5 Martensite Tempering in Dual‐Phase Steels
Examples
References
Further Reading
Problems
19 Heat‐Affected‐Zone Cracking
19.1 Hydrogen Cracking in Steels
19.1.1 Cause
19.1.2 Appearance
19.1.3 Susceptibility Tests
19.1.4 Remedies. 19.1.4.1 Preheating
19.1.4.2 Postweld Heating
19.1.4.3 Bead Tempering
19.1.4.4 Use of Low‐H Processes and Consumables
19.1.4.5 Use of Lower‐Strength Filler Metals
19.1.4.6 Use of Austenitic‐Stainless‐Steel Filler Metals
19.2 Stress‐Relief Cracking in Steels
19.3 Lamellar Tearing in Steels
19.4 Type‐IV Cracking in Grade 91 Steel
19.5 Strain‐Age Cracking in Ni‐Base Alloys
Examples
References
Further Reading
Problems
20 Heat‐Affected‐Zone Corrosion
20.1 Weld Decay of Stainless Steels
20.2 Weld Decay of Ni‐Base Alloys
20.3 Knife‐Line Attack of Stainless Steels
20.4 Sensitization of Ferritic Stainless‐Steel Welds
20.5 Stress Corrosion Cracking of Austenitic Stainless Steels
20.6 Corrosion Fatigue of Al Welds
Examples
References
Further Reading
Problems
21 Additive Manufacturing
21.1 Heat and Fluid Flow
21.2 Residual Stress and Distortion
21.3 Lack of Fusion and Gas Porosity
21.4 Grain Structure
21.5 Solidification Cracking
21.6 Liquation Cracking
21.7 Graded Transition Joints
21.8 Further Discussions
Examples
Example 21.1
Answer
Example 21.2
Answer
References
Further Reading
Problems
22 Dissimilar‐Metal Joining
22.1 Introduction
22.2 Arc and Laser Joining
22.2.1 Al‐to‐Steel Arc Brazing
22.2.1.1 Effect of Lap Joint Gap
22.2.1.2 Effect of Heat Input
22.2.1.3 Effect of Ultrasonic Vibration
22.2.1.4 Effect of Preheating
22.2.1.5 Effect of Postweld Heat Treatment
22.2.1.6 Butt Joint
22.2.2 Al‐to‐Steel Laser Brazing
22.2.3 Al‐to‐Steel Laser Welding
22.2.4 Mg‐to‐Steel Brazing
22.2.5 Al‐to‐Mg Welding
22.3 Resistance Spot Welding. 22.3.1 Al‐to‐Steel RSW
22.3.2 Mg‐to‐Steel RSW
22.3.3 Al‐to‐Mg RSW
22.4 Friction Stir Welding
22.4.1 Al‐to‐Cu FSSW
22.4.2 FSSW of Al to Galvanized Steel
22.4.3 Effect of Coating on Al‐to‐Steel FSSW
22.5 Other Solid‐State Welding Processes. 22.5.1 Friction Welding
22.5.2 Explosion Welding
22.5.3 Magnetic Pulse Welding
Examples
Answer
Answer
Answer
References
Further Reading
Problems
23 Welding of Magnesium Alloys
23.1 Spatter. 23.1.1 Spatter in Mg GMAW
23.1.2 Mechanism of Spatter
23.1.3 Elimination of Spatter
23.1.4 Irregular Weld Shape and Its Elimination
23.2 Porosity. 23.2.1 Porosity in Mg GMAW
23.2.2 Mechanisms of Porosity Formation and Elimination
23.2.3 Comparing Porosity in Al and Mg Welds
23.3 Internal Oxide Films. 23.3.1 Mechanism
23.3.2 Remedies
23.4 High Crowns
23.4.1 Mechanism of High‐Crown Formation
23.4.2 Reducing Crown Height
23.5 Grain Refining
23.5.1 Ultrasonic Weld Pool Stirring
23.5.2 Arc Pulsation
23.5.3 Arc Oscillation
23.6 Solidification Cracking
23.7 Liquation Cracking
23.7.1 A Simple Test for Crack Susceptibility
23.7.2 Effect of Filler Metals
23.7.3 Effect of Grain Size
23.8 Heat‐Affected Zone Weakening
Examples
Answer
Answer
Answer
Answer
References
Further Reading
Problems
24 Welding of High‐Entropy Alloys and Metal‐Matrix Nanocomposites
24.1 High‐Entropy Alloys. 24.1.1 Solidification Microstructure
24.1.2 Weldability
24.2 Metal‐Matrix Nanocomposites
24.2.1 Nanoparticles Increasing Weld Size
24.2.2 Nanoparticles Refining Microstructure
24.2.3 Nanoparticles Reducing Cracking During Solidification
24.2.4 Nanoparticles Allowing Friction Stir Welding
Examples
References
Further Reading
Problems
Appendix A Analytical Equations for Susceptibility to Solidification Cracking
Index
WILEY END USER LICENSE AGREEMENT
Отрывок из книги
Third Edition
Sindo Kou
.....
Sindo Kou
Madison, Wisconsin, 2020
.....