Industrial Environmental Management
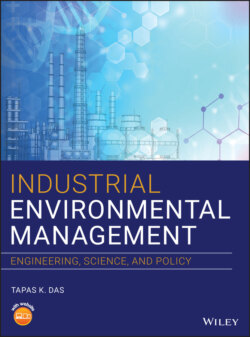
Реклама. ООО «ЛитРес», ИНН: 7719571260.
Оглавление
Tapas K. Das. Industrial Environmental Management
Table of Contents
List of Tables
List of Illustrations
Guide
Pages
Industrial Environmental Management. Engineering, Science, and Policy
About the Author
Preface
Acknowledgments
About the Companion Website
1 Why Industrial Environmental Management? 1.1 Introduction
1.1.1 ISO in Brief
1.1.2 ISO and the Environment
1.1.3 Benefits
1.2 Environmental Management in Industries
1.2.1 Environmental Challenges
1.3 Waste as Pollution
1.4 Defining Pollution Prevention
1.4.1 Resource Efficiency
1.5 The ZDZE Paradigm
1.6 Zero Discharge Industries
1.7 Sustainability, Industrial Ecology, and Zero Discharge (Emissions)
1.8 Why Zero Discharge Is Critical to Sustainability
1.9 The New Role of Process Engineers and Engineering Firms
Mini‐Case Study 1.1 Beer to Mushrooms: Focusing on the Productivity of Raw Materials
1.10 Zero Discharge (Emissions) Methodology
1.10.1 Analyze Throughput
1.10.2 Inventory Inputs and Outputs
1.10.3 Build Industrial Clusters
1.10.4 Develop Conversion Technologies
1.10.5 Designer Wastes
1.10.6 Reinvent Regulatory Policies
1.11 Making the Transition
1.11.1 Recycling of Materials and Reuse of Products
1.11.2 Dematerilization
1.11.3 Investment Recovery
1.11.4 New Technologies and Materials
1.11.4.1 New, Less Toxic Chemicals and Materials
Mini‐Case Study 1.2 DaimlerChrysler's ZD Wastewater Treatment Plant in Mexico
1.11.4.2 Improved Processes
1.11.5 New Mindset
1.11.5.1 System Design
1.11.5.2 Results
1.11.6 In the Full ZD (Emission) Paradigm
1.11.6.1 Opening New Opportunities
1.11.6.2 Providing Return on Investment
Mini‐Case Study 1.3 Recovery of Wastes from Palm Oil Extraction Yields High Return on Investment
1.12 Constraints and Challenges
1.12.1 The Challenges in Industrial Environmental Management
1.12.2 Codes of Ethics in Engineering
1.13 The Structure of the Book. 1.13.1 What Is in the Book?
Problems
References
2 Genesis of Environmental Problem Worldwide: International Environmental Regulations. 2.1 Introduction
2.1.1 Environmental History
2.2 Genesis of the Environmental Problem
2.3 Causes of Pollution and Environmental Degradation
2.3.1 Natural Causes
2.3.2 Man‐Made Causes
2.3.3 Population Growth
2.3.4 Poverty
2.3.5 Urbanization
2.4 Industrialization and Urbanization in the United States
2.4.1 Mini Case Studies
2.4.2 The Electrical Grid and Improvements in Transportation
2.4.3 Structural Steel and Skyscrapers
2.4.4 The Assembly Line
2.4.5 The Origins of Mass Production
2.5 Important Technological Developments
2.6 Industrial Disasters. 2.6.1 Bhopal: The World's Worst Industrial Tragedy
2.6.1.1 What Happened that Evening!
2.6.1.2 Taj Mahal Acid Rain Attack
2.6.1.3 River Ganges and River Yamuna
2.6.1.4 Flixborough
2.6.1.5 Love Canal Tragedy
2.6.1.6 Tennessee Valley Authority Kingston Coal Power Plant Toxic Ash Sludge Spill
2.6.1.7 Cuyahoga River Fire
2.6.1.8 The Great Smog of London
2.7 Environmental Law
2.7.1 History of Environmental Law
2.8 Pollution Control Laws. 2.8.1 Air Quality Law
2.8.2 Water Quality Law
2.8.3 Waste Management Law
2.8.4 Contaminant Cleanup Law
2.8.5 Chemical Safety Laws
2.8.6 Water Resources Law
2.8.7 Mineral Resources Law
2.8.8 Forest Resources Law
2.8.9 Wildlife and Plants Protection Laws
2.8.10 Fish and Game Laws
2.8.11 Principles
2.9 Resource Sustainability. 2.9.1 Environmental Impact Assessment
2.9.2 Sustainable Development
2.9.3 Equity
2.9.4 Transboundary Responsibility
2.9.5 Public Participation and Transparency
2.9.6 Precautionary principle
2.9.7 Prevention
2.10 Polluter Pays Principle
2.11 Theory/Environmental Law Debate
2.11.1 Environmental Impact Statement and NEPA Process
2.11.2 Purpose of NEPA
2.12 International Law
2.12.1 Africa
2.12.2 Asia
2.12.3 European Union
2.12.4 Middle East
2.12.5 Oceania
2.12.6 Australia
2.12.7 Brazil
2.12.8 Canada
2.12.9 China
2.12.10 Ecuador
2.12.11 Egypt
2.12.12 Germany
2.12.12.1 Environmental Rules for Doing Business in Germany: Legal Requirements
2.12.13 India
2.13 The Legal and Regulatory Framework for Environmental Protection in India. 2.13.1 Introduction
2.13.2 Legislation for Environmental Protection in India. 2.13.2.1 Water
2.13.2.2 Air
2.13.2.3 Forests and Wildlife
The Forest (Conservation) Act, 1980
2.13.3 General. 2.13.3.1 Environment (Protection) Act, 1986 (USEPA)
2.13.3.2 The Environment (Protection) Rules, 1986
2.13.3.3 The National Environment Appellate Authority Act, 1997
2.13.4 Hazardous Wastes
2.13.4.1 Factories Act, 1948 and Its Amendment in 1987
2.13.4.2 Public Liability Insurance Act (PLIA), 1991
2.13.4.3 National Environment Tribunal Act, 1995
2.13.5 International Agreements on Environmental Issues
2.13.5.1 Convention on International Trade in Endangered Species (CITES), of Wild Fauna and Flora, 1973
2.13.5.2 Montreal Protocol on Substances that Deplete the Ozone Layer (to the Vienna Convention for the Protection of the Ozone Layer), 1987
2.13.5.3 Basel Convention on Transboundary Movement of Hazardous Wastes, 1989
2.13.5.4 UN Framework Convention on Climate Change (UNFCCC), 1992
2.13.5.5 Convention on Biological Diversity, 1992
2.13.5.6 UN Convention on Desertification, 1994
2.13.5.7 International Tropical Timber Agreement and the International Tropical Timber Organization (ITTO), 1983, 1994
2.13.6 An Assessment of the Legal and Regulatory Framework for Environmental Protection in India
2.13.7 Emerging Environmental Challenges
2.13.7.1 Japan
2.13.7.2 New Zealand
2.13.7.3 Russia
2.13.7.4 South Africa
2.13.7.5 United Kingdom
History
2.14 United States Environmental Law
2.14.1 Scope
2.14.2 History
2.14.3 Legal Sources
2.14.4 Federal Regulation
2.14.5 Judicial Decisions
2.14.6 Common Law
2.14.7 Administration
2.14.8 Enforcement
2.14.9 Education and Training
2.14.10 Vietnam
2.15 ISO 9000 and 14000
2.15.1 Green Accounting Practices and Other Quality Manufacturing and Business Management Paradigms
Advantages
Disadvantages
Example 2.1
Solution
Example 2.2
Solution
2.16 Current Environmental Regulatory Development in the United States: From End‐of‐Pipe Laws and Regulations to Pollution Prevention. 2.16.1 Introduction
2.17 Greenhouse Gases
2.17.1 Nine Prominent Federal Environmental Statues
Examples (Multiple Choice) Example 2.3
Example 2.4
Example 2.5
Solution
Example 2.6
Solution
Example 2.7
Solution
Example 2.8
Solution
Example 2.9
Solution
Problems
References
3 Industrial Pollution Sources, Its Characterization, Estimation, and Treatment. 3.1 Introduction
3.2 Wastewater Sources. 3.2.1 Point Source
3.2.2 Nonpoint Source
3.3 Wastewater Characteristics
3.3.1 Physical Characteristics
3.3.2 Total Suspended Solids
3.3.3 Color
3.3.4 Odor
3.3.5 Temperature
3.4 Chemical Characteristics. 3.4.1 Inorganic Chemicals
3.4.2 Organic Chemicals
3.4.3 Volatile Organic Compounds
3.4.4 Heavy Metal Discharges
3.4.5 Some Inorganic Pollutants of Concern
3.4.6 Organic Pollutants of Concern
3.4.7 Thermal Pollution
3.5 Industrial Wastewater Variation. 3.5.1 Pollution Load and Concentration
3.5.2 Industrial Pretreatment
3.6 Industrial Wastestream Variables. 3.6.1 Dilute Solutions
3.6.2 Concentrated Solutions
3.7 Concentration vs. Mass of the Pollution
3.7.1 Frequency of Generation and Discharge
3.7.2 Hours of Operation vs. Discharge
3.7.3 Discharge Variations
3.7.4 Continuous and Intermittent Discharges
3.7.5 Industrial Effluents
3.7.6 Wastewater Quality Indicators: Selected Pollution Parameters. 3.7.6.1 Solids
3.7.6.2 Oxygen
3.7.6.3 Biochemical and Chemical Oxygen Demands
3.7.6.4 COD
3.7.6.5 Nitrogen
3.7.6.6 Phosphates
3.7.6.7 Pollutant Concentration and Loading in Wastewater
Conversion of mg/l (ppm) to lb/MG
Example 3.1
Solution
Example 3.2
Solution
3.8 Industrial Wastewater Treatment. 3.8.1 Variation in Industrial Wastewaters
3.8.2 Pretreatment Program Purpose
3.8.2.1 Pretreatment Specific Goals
3.8.3 Dental Waste Pretreatment Management
3.9 Air Quality
3.9.1 The Atmosphere
3.9.2 Unpolluted Air
3.9.3 Mobile Sources and Emission Inventory
3.9.4 Inventory Techniques
3.9.5 Data Reduction and Compilation
3.9.6 Major Sources of Air Emissions. 3.9.6.1 US Clean Air Act and Amendments
3.9.7 1990 Clean Air Act Amendments
3.9.8 Introduction to Air Pollution Control and Estimating Air Emission Rates
3.9.8.1 Air Emission Estimates
3.9.8.2 Emission Factors
3.9.8.3 What Is an AP‐42 Emission Factor?
3.9.8.4 AP‐42 by Chapters: Emission Factors for Quantifications
Example 3.3 Use of Emission Factors
Solution
3.9.8.5 Criteria Air Pollutants
3.9.8.6 NAAQS for Criteria Pollutants
3.9.8.7 Hazardous Air Pollutants
3.9.8.8 National Emission Standards for Hazardous Air Pollutants
3.9.8.9 Fugitive Emissions
3.9.8.10 Methods for Estimating Fugitive Emissions
Example 3.4 Estimating Fugitive Emissions Using Emission Factors
Solution
3.10 The Ideal Gas Law and Concentration Measurements in Gases
Example 3.5
Solution
Solution
Example 3.6
Solution
Example 3.7
Solution
3.11 Other Applications of the Ideal Gas Law
Example 3.8
Solution
Example 3.9
Solution
Example 3.10
Solution
3.12 Gas Flow Measurement
Example 3.11
Solution
3.13 Flow at Standard Temperature and Pressure
3.14 Gas Flowrate Conversion from SCFM to ACFM. Example 3.12
Solution
3.15 Corrections for Percent O2
3.16 Boiler Flue Gas Concentrations Are Usually Corrected to 3% Oxygen. Example 3.13
Solution
3.17 Air‐to‐Fuel Ratio and Stoichiometric Ratio
Example 3.14
Solution
3.18 Material Balances and Energy Balances
Example 3.15 A Mass Balance Problem on HAPs
Solution
Example 3.16 Heat Recovery and Save Money
Solution
Example 3.17 Hazardous Waste Mass Balance for Meeting Regulatory Criterion
Solution
Example 3.18
Given:
Solution
3.19 Wastes in the United States
3.19.1 Industrial Wastes Management Approach
3.19.2 Waste as Pollution
3.19.3 Why Recycle?
3.19.4 Chemical Waste
3.19.5 Electronic Waste
3.20 Hazardous Waste
3.20.1 Hazardous Wastes in the United States of America
3.20.2 Hazardous Waste Mapping Systems
3.20.3 Universal Wastes
3.20.4 Final Disposal of Hazardous Waste
3.20.5 Recycling
3.20.6 Portland Cement
3.21 Incineration, Destruction, and WtE
3.22 Hazardous Waste Landfill (Sequestering, Isolation, etc.)
3.22.1 Pyrolysis
3.23 Radioactive Waste
3.23.1 Sources
3.23.2 Nuclear Fuel Cycle. 3.23.2.1 Front End
3.23.2.2 Back End
3.23.2.3 Nuclear Industry
3.24 Coal
3.24.1 Oil and Gas
3.25 Low‐Level Waste
3.25.1 Intermediate‐Level Waste
3.25.2 High‐Level Waste
3.25.3 Transuranic Waste
3.26 Nuclear Waste Management
3.26.1 Initial Treatment. 3.26.1.1 Vitrification
3.26.1.2 Ion Exchange
Problems
References
4 Industrial Wastewater, Air Pollution, and Solid and Hazardous Wastes: Monitoring, Permitting, Sample Collections and Analyses, QA/QC, Compliance with State Regulations and Federal Standards. 4.1 Introduction
4.2 Industrial Process Water
4.3 Common Elements, Radicals, and Chemicals in Water Analysis
Examples 4.1
Solution
4.4 Purposes and Objectives for Inspecting and Sampling
4.4.1 Analytical Methods
4.4.2 State Waste Discharge Permit
4.4.3 NPDES Wastewater Discharge Permit
4.4.4 General Wastewater Discharge Permit
4.4.4.1 Wastewater Flow Rate
4.4.4.2 Quality Assurance
4.5 Sampling and QA/QC Plan
4.5.1 QA/QC Procedures
4.5.2 QA Procedures for Sampling
4.5.3 QC Procedures for Sampling
4.5.3.1 Blanks
4.5.3.2 Field Duplicate
4.5.3.3 Split Samples
4.5.4 Laboratory QA/QC
4.5.5 Sampling Location
4.5.6 Type of Sample
4.5.6.1 Grab Samples
4.5.6.2 Composite Samples
4.5.7 Continuous Monitoring
4.5.8 Sample Preservation and Holding Times
4.5.9 Sample Documentation
4.5.10 General Documentation Procedures
4.5.11 COC Procedures
4.5.12 Sample Identification and Labeling
4.5.13 Sample Packaging and Shipping
4.6 Whole Effluent Toxicity Testing. 4.6.1 Introduction
4.6.2 The WET Testing
4.6.3 Toxicity Testing and Evaluation of Toxicity Test Results
Example 4.2
Solution
4.6.4 Toxic Units
4.6.5 Application of Toxicity Test Results
4.6.6 Protection Against Acute Toxicity
4.6.7 Protection Against Chronic Toxicity
Example 4.3
Solution
4.7 Flow Measurements
4.7.1 Open Channel Flow
4.7.1.1 Primary Devices
Example 4.4
Solution
Example 4.5
Solution
4.7.1.2 Secondary Devices
4.7.2 Closed Channel Flow
Example 4.6
Solution
4.7.3 Pitot Tube
Example 4.7
Solution in SI
4.7.4 Electromagnetic Flow Meter
4.8 The Point of Compliance with the Water Quality Standards
4.8.1 Mixing Zones
4.8.2 Streeter–Phelps Equation and DO Sag Curve in a River
4.8.3 Mixing of Wastewater in Rivers: Mass‐Balance Approach
Example 4.8
Solution
4.9 Water Quality Modeling
4.9.1 Formulations and Associated Constants
4.9.2 WWTP BOD, SS, and Fecal Coliform Removal Efficiencies: Meet Water Quality Standards
4.9.3 NPDES Wastewater Discharge Permits for Point Sources
Example 4.9
Solution
4.10 Example NPDES Permits (for Refinery and Aluminum Smelter are shown in Section D.1) 4.10.1 Total Maximum Daily Load (TMDL) Rule
Example 4.10 TMDL Calculation
4.11 Air Pollution Perspective
4.11.1 Causes, Sources, and Effects
4.11.2 Air Toxics: Toxic Air Pollutants
4.12 Prevention of Significant Deterioration (PSD) Permitting Process. 4.12.1 Introduction
4.12.2 The PSD Program Goals
4.13 An Overall Permitting Process
4.13.1 Who Needs a PSD Permit?
4.13.2 What Does the PSD Program Require of the Applicant?
4.14 Best Available Control Technology. 4.14.1 Introduction
4.14.2 Control Technology Requirement Definitions
There Are Several Different Control Technology Requirements
4.14.2.1 Reasonably Available Control Technology
4.14.2.2 Best Available Retrofit Control Technology
4.14.2.3 Maximum Achievable Control Technology
4.14.2.4 LAER
4.14.2.5 Generally Available Control Technology
4.14.2.6 Toxic Best Available Control Technology
4.14.2.7 Reasonably Available Control Measures and Best Available Control Measures
4.14.3 BACT Selection Strategy
4.14.4 Top‐Down BACT Analysis
4.14.5 Identify Technologies
4.14.6 Determine Technical Feasibility
4.14.7 Rank Technically Feasible Alternatives
4.14.8 Evaluate Impacts of Technology
4.14.8.1 Energy Impacts
4.14.8.2 Environmental Impacts
4.14.8.3 Cost Effectiveness
4.14.9 Plant‐Wide Applicability Limitation
4.15 Atmospheric Dispersion Modeling
4.15.1 Atmospheric Layers
Example 4.11
Solution
4.16 Dispersion Models: Indoor Concentrations
Example 4.12
Solution
4.16.1 Gaussian Dispersion Model
Example 4.13
Solution
4.16.2 Modeling Protocol
4.16.3 Dispersion Model Selection
4.16.3.1 AERSCREEN
4.16.3.2 AERMOD
4.16.4 CALPUFF
4.16.5 Attainment and Non‐Attainment Areas
4.17 State Implementation Plan
4.17.1 What National Standards must SIPs Meet?
4.17.2 What Is Included in a SIP?
4.17.3 Who Is Responsible for Enforcing a SIP?
4.18 Compliance. 4.18.1 Compliance Requirements
4.18.1.1 Methods to Determine Compliance
4.18.1.2 Direct Measurement of Air Emission Rates
Example 4.14
Solution
Example 4.15
Solution
Example 4.16
Solution
4.18.1.3 Monitoring
4.18.1.4 Opacity Monitoring
4.18.1.5 Record Keeping
4.18.1.6 Reporting
4.18.1.7 Good Conduct Provisions
4.19 CAA Enforcement Provisions
Civil Penalties Can Be Assessed Under the Clean Air Act
4.19.1 Administrative Penalty Orders
4.19.2 Issuing an Order Requiring Compliance or Prohibition
4.19.3 Bringing Civil Action in Court
4.19.4 Requesting the Attorney General to Bring Criminal Action
The Clean Air Act Also Provides for Criminal Enforcement Including Imprisonment
4.19.5 Emergency as a Defense
4.19.6 Section 114: Fact‐Finding
Section 114 Is Fact‐Finding in Anticipation of Prosecution
4.19.7 Inspection Protocol
4.19.8 Continuous Emission Monitoring
4.19.8.1 Operation
4.19.9 QA and QC in Air Emission Rates
4.19.10 Performing Stack Tests
Example 4.17 Calculations for Standard Volume
Solution
Example 4.18 Stack Velocity
Solution
4.20 Industrial Solid Wastes and Its Management. 4.20.1 Solid Waste Treatment: Some Perspectives on Recycling
4.20.2 Why Recycle?
4.20.3 What Is Recycling
4.20.4 A Brief Overview of Recycling in the United States and United Kingdom
4.20.5 Recycling Today
4.20.6 Recycling as a Route to Sustainable Productivity and Growth
4.20.7 Resource Conservation and Recovery Act
4.20.7.1 History and Goals
4.20.7.2 RCRA Implementation
4.20.7.3 Identification and Characterization of Hazardous Waste
4.20.7.4 Characteristics
4.20.7.5 Listed Hazardous Wastes
4.20.8 Few RCRA Provisions: Cradle–to‐Grave Requirements
4.20.8.1 Nonhazardous Solid Wastes
4.20.8.2 Underground Storage Tanks. Background
4.20.8.3 Transportation of Hazardous Waste
4.20.9 TSDFs Permits
4.20.9.1 Recycling
4.20.9.2 Portland Cement
4.20.9.3 Incineration, Destruction, and Waste‐to‐Energy
Example 4.19
Solution
4.20.9.4 Pyrolysis
Example 4.20
Solution
4.21 Hazardous Waste Landfill (Sequestering, Isolation, etc.)
4.21.1 Final Disposal of Hazardous Waste
Example 4.21
Solution
4.22 Industrial Waste Generation Rates
4.22.1 Generator Requirements and Responsibilities
4.22.2 Environmental Audits
4.23 Comprehensive Environmental Response, Compensation, and Liability Act and Superfund
4.23.1 History
4.23.2 Provisions
4.23.3 Procedures
4.23.4 Implementation
4.23.5 Hazard Ranking System
4.23.6 Environmental Discrimination
4.23.7 Case Studies in African American Communities
4.23.8 Case Studies in Native American Communities
4.24 Industrial Waste Management in India: Shifting Gears
4.24.1 Integrated Solid Waste Management
4.24.2 Hazardous Waste Handling and Management Rule
4.24.3 Biomedical Waste Rule
4.24.4 E‐Waste Rule
4.24.5 Plastic Nonhazardous Waste Rule
Problems
References
5 Assessment and Management of Health and Environmental Risks: Industrial and Manufacturing Process Safety
5.1 Health Risk Assessment
5.1.1 Air Pollution
5.1.2 Problem Formulation
Example 5.1 Monitoring
Solution
Example 5.2 Continuous Monitoring
Solution
5.1.3 Exposure Assessment
5.1.3.1 Partition Coefficient and Bioconcentration Factor
Example 5.3 Predicting Bioconcentration
Solution
Example 5.4 Use of Slope Factors
Solution
5.1.3.2 Exposure Point Concentrations
5.1.3.3 Mechanistic Models
5.1.3.4 Receptor Doses
Example 5.5 Calculation of Contaminant Intake
Solution
Example 5.6 Average Daily Intake from Dermal Contact with Soil
Solution
5.1.4 Toxicity Assessment
5.1.5 Risk Characterization
5.1.5.1 Risk for Average and Maximum Exposures
5.1.5.2 Carcinogenic Risk
5.2 Assessing the Risks of Some Common Pollutants
Example 5.7 Cancer Risk Assessment
Solution
5.2.1 NOx, Hydrocarbons, and VOCs: Ground‐Level Ozone
5.2.1.1 Smog Formation
5.2.2 Carbon Monoxide
Example 5.8 Total Weighted Average Concentration
Solutions
5.2.3 Lead and Mercury
Example 5.9 Mercury Removal
Solution
Example 5.10 Inhalable PCBs and PAHs
Solution
5.2.4 Particulate Matter
5.2.4.1 Visibility Impairment
5.2.5 SO2, NOx, and Acid Deposition
5.2.6 Air Toxics
5.3 Ecological Risk Assessment
5.3.1 Technical Aspects of Ecological Problem Formulation
5.3.1.1 Site Conceptual Models
5.3.1.2 Identifying Endpoints
5.3.1.3 Selecting Measurement Endpoints
5.3.2 Ecological Exposure Assessment
5.3.2.1 Fish Community
5.3.2.2 Benthic Macroinvertebrate Community
5.3.2.3 Soil Invertebrate Species
5.3.2.4 Terrestrial Plants
5.3.2.5 Terrestrial Wildlife
5.3.3 Ecological Effects Assessment
5.3.3.1 Fish Community
5.3.3.2 Benthic Community
5.3.3.3 Soil Invertebrate and Plant Communities
5.3.3.4 Wildlife
5.3.4 Additional Components of Ecological Risk Assessments
5.3.4.1 Sampling and Surveys
5.3.4.2 Field Sampling
5.3.4.3 Field Surveys
5.3.4.4 Speciation
5.3.4.5 Sources of Other Effects Information
5.3.4.6 Additional Effects that Figure in Many ERAs. Global Warming
5.3.5 Tropospheric Ozone Pollution and Its Effects on Plants
5.3.5.1 Visibility and Regional Haze
5.3.5.2 Eutrophication: A Widespread Ecological Effect
5.3.6 Toxicity Testing
5.3.6.1 Evaluation of Toxicity Test Results
5.3.6.2 Ecological Risk Characterization
5.4 Risk Management
5.4.1 Valuation of Ecological Resources
5.4.1.1 Utilitarian
Commodity Values
Potential Commodity Values
Recreation
Services of Nature
5.4.1.2 Nonutilitarian
Existence
Aesthetic
Scientific
Cultural and Ethical
5.4.2 Modeling Risk Management
5.4.3 Other Considerations for Risk Characterization
5.4.4 Conceptual Bases for De Minimis Risks
5.4.5 Ecological Risk Assessment of Chemicals. 5.4.5.1 One‐Dimensional Models
5.4.5.2 Two‐Dimensional Models. Concentration/Response
Time–Response Functions
Time–Concentration
“Acute” and “Chronic” as Temporal Categories
Concentration and Duration as Replacement for Concentration and Time
Worst Case
Finding a Middle Ground
Dose–Response Functions
5.4.5.3 Three‐Dimensional Models
5.4.5.4 Plastic Waste Choking Oceans, Rivers, Landfills
5.5 Communicating Information on Environmental and Health Risks
5.5.1 From Concern to Outrage: Determinants of Public Response
5.5.2 Sustainable Strategies for Environmental and Health Risk Communication
5.5.2.1 Breaking Down the Barriers to Communication
We're Too Small to Do Outreach
Our Facilities and Operations Are Environmentally Sound
If We Talk to People, They Will Just Get Upset
Our People Are Already Overworked
5.5.2.2 Building a Communication Program
5.5.3 Case Study: Environmental and Health Risk Communication Neglected Until After an Accident
5.5.3.1 The Accident and Aftermath
5.5.3.2 The Costs of Noncommunication
5.5.4 Lessons Learned
5.6 Environmental Information Access on the Internet
5.6.1 Internet Sources. 5.6.1.1 EPA's Integrated Risk Information System
5.6.1.2 EPA Chemical Accident Histories and Investigations
5.6.1.3 International Toxicity Estimates for Risk database
5.6.1.4 AIRNow's Links to Real‐Time Air Pollution Data
5.6.1.5 Air and Waste Management Association's State Agency Listing
5.6.1.6 Acid Rain, Atmospheric Deposition and Precipitation Chemistry
5.6.1.7 Predict Mixed Chemicals' Reactions
5.6.1.8 Model an Oil Spill
5.6.1.9 Hazards Analysis for Toxic Substances, Version 3
5.6.1.10 EPA Center for Exposure Assessment Modeling
5.6.1.11 Regulatory Air Models
5.6.1.12 EPA's Risk Management Consequence Analysis (RMP*Comp)
5.6.1.13 Agency for Toxic Substances and Disease Registry's Primer on Health Risk Communication
5.6.1.14 Disaster Communication from Indiana Law University
5.6.1.15 EPA's National Service Center for Environmental Publications
5.6.1.16 The National Academies' Reports Online
5.6.2 Implications and Limitations of Using the Internet
5.7 Health and Occupational Safety. 5.7.1 Occupational Safety and Health Administration
5.7.1.1 “Right‐To‐Know” Laws
5.7.1.2 National Institute of Occupational Safety and Health
5.7.1.3 Material Safety Data Sheets
5.7.1.4 Integrated Risk Information System
5.7.1.5 Nanotechnology Legislation
5.8 Industrial Process Safety System Guidelines
5.8.1 Types of Safety Systems
5.8.1.1 Emergency Shutdown System
5.8.1.2 Safety Shutdown System
5.8.1.3 Fire and Gas System
5.8.1.4 Emergency Depressurization Systems
5.8.1.5 Pressure Safety Valves
5.9 Industrial Hygiene
5.9.1 Toxicology
5.9.2 TLVs and Exposure Limits
5.10 Atmospheric Hazards
5.10.1 Oxygen Deficient Atmosphere
5.10.2 Toxic Atmosphere
5.10.3 Chronic Industrial Exposure
5.10.4 Accidental Chlorine Gas Release: Case Study
5.10.5 Determination of Toxic Endpoint Distance
5.10.6 Determination of Exposed Population to this Scenario
5.10.7 Chronic Industrial Exposure: TWA and TLV
Example 5.11
Solution
Example 5.12
5.11 Safety Equipment
5.11.1 Personal Protective Equipment
5.11.1.1 Heat Exposures
5.11.1.2 Electric Exposures
5.11.1.3 Chemical Exposures
5.11.1.4 Inhalation Risks
5.11.1.5 Eye Risks
5.11.2 Personal Protective Clothing
5.12 Communication Devices
5.12.1 Air Monitoring Devices
5.12.1.1 Estimate of Dilution Air
5.12.2 Ventilation Devices
Example 5.13
Solution
Example 5.14
Solution
5.12.3 Safety Harness and Retrieval System
5.12.4 Respirators
5.12.5 Confined Space Entry
5.12.6 Safety Training
5.13 Noise
5.13.1 Occupational Noise Exposure
5.13.2 Basics of Occupational Noise and Hearing Protection
5.13.3 Noise: Physical Principles
Example 5.15 Sound Pressure/Intensity Relationship
Solution
5.13.4 Noise Exposure and Noise Protection
Example 5.16 Noise Exposure
Solution
5.13.5 Noise Control
Example 5.17 Noise Control
Solution
5.14 Radiation. 5.14.1 Definition
5.14.2 Different Sources of Radiation
5.14.3 External Exposure and Internal Exposure
5.14.4 Radionuclide Decay
Example 5.18 Radioactive decay
Solution
5.14.5 Radiation Dose
5.14.5.1 Radiation Dose Units. Exposure Dose: The Roentgen
Absorbed Dose: The Gray
5.14.6 Biological Effects of Ionizing Radiation
Example 5.19 Biological Half‐Life
Solution
5.14.7 Radiation Protection Principles
5.14.7.1 Reduction of External Radiation Hazards
Shielding
Distance
Reduction of Exposure Time
Example 5.20 Lead Thickness
Solution
Example 5.21 Concrete Thickness
Solution
Example 5.22 Radioactive Decay
Solution
Example 5.23 Radioactive Decay
Solution
5.15 Effects of Global Warming: Climate Change – The World's Health
5.15.1 The Greenhouse Effect
5.15.2 Greenhouse Gases
Example 5.24 Calculating GHG Mass‐Based and CO2e (Equivalent)‐Based Emissions
Example 5.25 CO2 emission from cars
Solution
5.15.3 Are the Effects of Global Warming Really Concerns for Our Future?
5.15.4 More Frequent and Severe Weather
5.15.5 Higher Death Rates
5.15.6 Dirtier Air
5.15.7 Higher Wildlife Extinction Rates
5.15.8 More Acidic Oceans
5.15.9 Higher Sea Levels
5.15.10 Effects of Global Warming on Humans
5.16 Key Vulnerabilities. 5.16.1 Health
5.16.2 Extreme Weather Events
5.16.3 Environment
5.16.4 Temperature
5.16.5 Water
5.16.6 Social Effects of Extreme Weather
5.17 Energy Sector. 5.17.1 Oil, Coal, and Natural Gas
5.17.2 Nuclear
5.17.3 Hydroelectricity
5.17.4 Transport
Problems
References
6 Industrial Process Pollution Prevention: Life‐Cycle Assesvsment to Best Available Control Technology. 6.1 Industrial Waste
6.1.1 Waste as Pollution
6.1.2 Pollution Prevention in Industries
6.1.3 Defining Process Pollution Prevention (P3)
6.2 What Is Life Cycle Assessment?
6.2.1 Benefits of Conducting an LCA
6.2.2 Limitations of LCAs as Tools
6.2.3 Conducting an LCA
6.2.3.1 Goal Definition and Scoping
6.2.3.2 Define the Goal(s) of the Project
6.2.3.3 Determine the Type of Information Needed to Inform the Decision‐Makers
6.2.3.4 Determine How the Data Should Be Organized and the Results Displayed
6.2.3.5 What Will and Will not Be Included
Raw Materials Acquisition
Manufacturing
Use/Reuse/Maintenance
Recycle/Waste Management
6.2.3.6 Accuracy Required of the Data
6.2.3.7 Ground Rules for Performing the Work
6.2.4 Life Cycle Inventory
6.2.4.1 Step 1: Develop a Flow Diagram
6.2.4.2 Step 2: Develop an LCI Data Collection Plan
6.2.4.3 Step 3: Collect Data
6.2.4.4 Step 4: Evaluate and Document the LCI Results
6.2.5 Life Cycle Impact Assessment
6.2.5.1 Why Conduct an LCIA?
6.2.5.2 Key Steps of a LCIA
Step 1: Select and Define Impact Categories
Step 2: Classification
Step 3: Characterization
Step 4: Normalization
Step 5: Grouping
Step 6: Weighting
Step 7: Evaluate and Document the LCIA Results
6.2.6 Life Cycle Interpretation
6.2.6.1 Key Steps to Interpreting the Results of the LCA
Step 1: Identify Significant Issues
Step 2: Evaluate the Completeness, Sensitivity, and Consistency of the Data
Step 3: Draw Conclusions and Recommendations
6.2.6.2 Reporting the Results
6.2.6.3 Conclusion
6.3 LCA and LCI Software Tools
6.3.1 ECO‐it 1.0
6.3.2 EcoManager
6.3.3 Eco Bat 2.1
6.3.4 GaBi 4
6.3.5 IDEMAT
6.3.6 EIOLCA
6.3.7 LCAD
6.3.8 LCAiT
6.3.9 REPAQ
6.3.10 SimaPro 7
6.3.11 TEAM (Tool for Environmental Analysis and Management)
6.3.12 TRACI: A Model Developed by the USEPA
6.3.13 Umberto NXT CO2
6.3.14 International Organizations and Resources for Conducting Life Cycle Assessment
6.4 Evaluating the Life Cycle Environmental Performance of Chemical‐, Mechanical‐, and Bio‐Pulping Processes. 6.4.1 Introduction
6.4.2 Application of LCA
6.4.3 The Pulping Processes. 6.4.3.1 Mechanical Pulping
6.4.3.2 Chemical Pulping Processes
6.4.3.3 Biopulping: A Review of a Pilot Project
6.4.3.4 Introduction to Biopulping
6.4.3.5 Large‐Scale Implementation of Biopulping
6.4.3.6 Economics and Environmental Benefits of the Biopulping Process
6.4.3.7 Quantitative Analyses Using the USEPA Model: TRACI
6.4.3.8 Model Input and Output
6.5 Evaluating the Life Cycle Environmental Performance of Two Disinfection Technologies
6.5.1 The Challenge
6.5.2 The Chlorination (Disinfection) Process
6.5.2.1 Limitations
6.5.2.2 Human Health and Environmental Impact
6.5.3 Dechlorination with Sulfur Dioxide
6.5.3.1 Limitations
6.5.3.2 Environmental Impact
6.5.3.3 Effects of Chlorine on Aquatic Life
Results of Laboratory Bioassays
6.5.4 UV Disinfection Process
6.5.4.1 UV Transmission or Absorbance
6.5.4.2 Disinfection Standards
6.5.4.3 Operation, Maintenance, and Worker Safety
6.5.4.4 Costs
6.5.4.5 Environmental Impacts of Energy Sources and Implications of Renewables
6.6 Case Study: LCA Comparisons of Electricity from Biorenewables and Fossil Fuels
6.6.1 Results. 6.6.1.1 System Energy Balance
6.6.1.2 Global Warming Potential
6.6.1.3 Air Emissions
6.6.1.4 Resource Consumption
6.6.2 Sensitivity Analysis
6.6.3 Summary and Conclusions
6.7 Best Available Control Technology (for Environmental Remediation)
6.7.1 What Is “Best Available Control Technology”?
6.7.1.1 Reasonably Available Control Technology
6.7.1.2 Lowest Achievable Emissions Rate
6.7.1.3 Life Cycle‐Based Environmental Law
6.7.1.4 Life Cycle Best Control Technology
6.8 BACT: Applications to Gas Turbine Power Plants
6.8.1 Importance of Energy Efficiency
6.8.2 NOx BACT Review. 6.8.2.1 Combustion Turbines and Duct Burners
6.8.2.2 SCONOX
6.8.2.3 XONON
6.8.2.4 Selective Catalytic Reduction
6.8.2.5 Lean‐Premix Technology or Dry‐Low NOx
6.8.2.6 Steam/Water Injection
6.8.2.7 Summary of NOx BACT for Turbines and Duct Burners
6.8.3 CO BACT Review: Combustion Turbines and Duct Burners
6.8.3.1 Catalytic Oxidation
6.8.3.2 Good Combustion Practices
6.8.3.3 Combustion Control
6.8.3.4 Summary of CO BACT for Turbines and Duct Burners
6.8.4 BACT Evaluation for PM/PM10 Emissions
6.8.4.1 Step 1: Identify Potential Control Technologies
6.8.4.2 Step 2: Eliminate Technically Infeasible Options
6.8.4.3 Electrostatic Precipitators
6.8.4.4 Fabric Filters
6.8.4.5 Step 3: Ranking of Remaining Control Technologies by Control Effectiveness
6.8.4.6 Step 4: Evaluation of the Most Effective Emissions Controls
6.8.4.7 Step 5: Select BACT for the Control of PM/PM10 Emissions
6.8.5 VOC Control Technologies
6.8.5.1 Catalytic Oxidation
6.8.5.2 Good Combustion Practices
6.8.6 BACT Evaluation for SO2 and H2SO4 Emissions
6.8.6.1 Step 1: Identify Potential Control Technologies
6.8.6.2 Step 2: Eliminate Technically Infeasible Options
6.8.6.3 Step 3: Ranking of Remaining Control Technologies by Control Effectiveness
6.8.6.4 Step 4: Evaluation of the Most Effective Emissions Controls
6.8.6.5 Step 5: Select BACT for the Control of SO2 Emissions
Problems
References
7 Economics of Manufacturing Pollution Prevention: Toward an Environmentally Sustainable Industrial Economy. 7.1 Introduction
7.2 Economic Evaluation of Pollution Prevention
7.2.1 Total Cost Assessment of Pollution Control and Prevention Strategies
7.2.2 Economics of Pollution Control Technology
7.3 Cost Estimates
7.3.1 Elements of Total Capital Investment
7.3.2 Elements of Total Annual Cost
7.4 Economic Criteria for Technology Comparisons
7.5 Calculating CF
Example 7.1 Total Capital Cost
Solution
Example 7.2 Cost‐Effectiveness Calculation
Solution
7.5.1 Achieving a Responsible Balance
7.6 From Pollution Control to Profitable Pollution Prevention
7.6.1 Life Cycle Costing
7.6.2 Total Cost Assessment
7.6.3 Economic Consideration Associated with Pollution Prevention
7.7 Resource Recovery and Reuse
7.8 Profitable Pollution Prevention in the Metal‐Finishing Industry
7.8.1 National Metal Finishing Strategic Goals Program
7.8.2 The Role of Pollution Prevention Technologies. 7.8.2.1 Moving Toward the Zero Discharge Goal
7.8.2.2 Planning and Implementation
7.8.2.3 Practicing Pollution Prevention
Mini‐Case Study (USEPA 1998): A Water Management P2Example
7.8.2.4 Case Study: An Emerging Profitable Pollution Prevention Technology
Description
7.8.2.5 Environmental Benefit
7.8.2.6 Economic Benefit
7.8.2.7 Technology Transferability
7.8.3 Value‐Added Chemicals from Pulp Mill Waste Gases
7.8.4 Recovery and Control of Sulfur Emissions
7.8.4.1 Freshwater Use Reduction and Chemical Recovery and Reuse Save Million at Pulp Mill. Effluent Discharges
7.8.4.2 Brine Concentrator for Recycling Wastewater
Mini‐Case Study. Saving the Colorado River
7.8.4.3 Economics of Brine Concentrator Systems
Mini‐Case Study. Calculating Payback for a Zero Discharge System
7.9 Use of Treated Municipal Wastewater as Power Plant Cooling System Makeup Water: Tertiary Treatment vs. Expanded Chemical Regimen for Recirculating Water Quality Management. 7.9.1 Introduction
7.9.2 Key Points
7.9.3 The World's First Zero Effluent Pulp Mill at Meadow Lake: The Closed‐Loop Concept
7.9.3.1 Clarification
7.9.3.2 Evaporation
7.9.3.3 Concentration
7.9.3.4 Stripping
7.9.3.5 Incineration
7.9.4 Successful Implementation of a Zero Discharge Program
7.9.4.1 Closing the Loop
7.9.5 Conclusions
7.10 Consequences of Dirty Air: Costs–Benefits
7.10.1 Public Health
7.10.2 Visibility
7.10.3 Ecosystems
7.10.4 Economic Consequences
7.10.5 Global Climate Change
7.10.6 Quality of Life
7.10.7 Costs–Benefits Analysis
7.11 Some On‐Going Pollution Prevention Technologies
Example 7.3 Solvent Emission from a Dry Cleaning Shop
Solution
Example 7.4 Cost of a Catalytic/Thermal Incinerator
Solution
7.11.1 Economic Performance Indicators
7.11.2 Estimates of Environmental Costs
Example 7.5 Potential Pollution Control Costs for Greenhouse Gases
Solution
7.11.3 Total Annualized Cost for BACT
7.11.4 Cost Per Ton (T) of Pollutant Removal
Example 7.6 Multi‐Cyclone
Example 7.7 Venturi Scrubber
Example 7.8 Electrostatic Precipitator
Example 7.9 Fabric Filter
7.12 Cost Indices and Estimating Cost of Equipment
Example 7.10
Solution
7.12.1 Equipment Costs
Example 7.11
Solution
Example 7.12
Solution
7.13 Waste‐to‐Energy
7.13.1 Methods. 7.13.1.1 Incineration
7.13.2 Other Technologies
7.13.3 Global Developments
7.13.3.1 Carbon Dioxide Emissions
7.13.4 Examples of WtE Plants
7.13.5 Case Study: Energy Recovery from Municipal Solid Waste: Profitable Pollution Prevention at the City of Spokane, Washington (see Appendix G) Example 7.13 Waste‐to‐Energy
Solution
Example 7.14 Waste‐to‐Energy
Solution
7.14 Sustainable Economy and the Earth
7.14.1 What Is a Sustainable Economy?
7.14.2 Costs of Manufacturing Various Biobased Products and Energy
7.14.2.1 Electricity from Combustion of Biomass
7.14.2.2 Electricity from Gasification of Biomass
7.14.2.3 Biogas from Anaerobic Digestion
7.14.2.4 Ethanol from Biomass
7.14.2.5 Methanol from Biomass‐Derived Syngas
7.14.2.6 Bio‐Oil from Fast Pyrolysis
7.14.2.7 Biodiesel from Vegetable Oils
7.14.2.8 Succinic Acid
7.14.2.9 Lactic Acid
Problems
References
Notes
8 Lean Manufacturing: Zero Defect and Zero Effect: Environmentally Conscious Manufacturing
8.1 Introduction
8.2 Engineering Data Summary and Presentation
8.2.1 Sample Mean
Example 8.1
Solution
Example 8.2
Solution
8.2.2 Stem‐and‐Leaf Diagram
8.2.3 Constructing a Stem‐and‐Leaf Display. Example 8.3
8.2.4 Application
8.2.5 Histogram
Example 8.4
Solution
8.2.6 Pareto Diagram
Example 8.5
Solution
8.2.7 Boxplots
Example 8.6
Solution
8.2.8 Statistical Tools for Experimental Design: Process and Product Development
8.3 Time Series: Process over Time
8.3.1 Basic Principles
8.4 Process Capability
8.4.1 Statistical Process Control
8.4.2 Control Charts for Variables
Example 8.7
Solution
8.4.3 PC Analysis
8.5 Lean Manufacturing
8.5.1 Overview
8.5.2 History: Pre‐Twentieth Century. 8.5.2.1 Benjamin Franklin
8.5.2.2 William Boeing
8.5.2.3 Frederick Winslow Taylor
8.5.2.4 Henry Ford
8.5.3 Toyota Develops TPS. 8.5.3.1 Sakichi Toyoda
8.5.4 Tata Group
8.6 Types of Waste
8.7 Six Sigma in Industry
8.8 Lean Implementation Develops from TPS. 8.8.1 Lean Leadership
8.8.2 Differences from TPS
8.8.3 Lean Services
8.8.4 Goal and Strategy
8.8.5 Examples: Lean Strategy in the Global Supply Chain and Its Crisis. 8.8.5.1 Strategy
8.8.5.2 Crisis
8.8.6 Steps to Achieve Lean Systems
8.8.6.1 Design a Simple Manufacturing System
8.8.6.2 Continuous Improvement
8.8.7 Measure
8.8.8 Implementation Dilemma
8.9 Manufacturing System Characteristics: Process Planning Basics
8.10 Design for Life Cycle
8.11 Sustainable Design and Environmentally Conscious Design and Manufacturing
8.11.1 Technologies for Sustainable Manufacturing
8.11.2 Green Manufacturing Pipeline
8.11.3 Sustainable Manufacturing: Is Green Equivalent to Sustainable?
8.11.4 Manufacturing Technology Wedges
8.12 Lean Six Sigma. 8.12.1 Introduction
8.12.2 The History of Six Sigma: 1980s–2000s. 8.12.2.1 Motorola Story
8.12.2.2 General Electric Story
8.12.2.3 DMAIC Model
The Phases of DMAIC
8.12.2.4 Calculating Process Sigma Values
8.12.2.5 Lean Six Sigma Organization Structure
8.12.3 5S
Japanese terms
English terms
8.13 Six Sigma and Lean Manufacturing
8.13.1 Comparing the Two Methodologies
8.14 Cost vs. Quality Analysis
8.14.1 Considerations
8.15 Assessing and Reducing Risk in Design: Cost to Manufacturer
8.16 The Heart and Soul of the Toyota Way: Lean Processes
8.16.1 Fourteen Principles of the Toyota Way. 8.16.1.1 Long‐Term Philosophy
8.16.1.2 Lean Processes: The Right Process will Produce the Right Results
8.16.1.3 Develop and Challenge Your People and Partners Through Long‐term Relationships
8.16.1.4 Problem Solving and Continuous Improvement Drive Organizational Learning
8.16.2 Life Cycle Cost Analysis (LCCA)
8.16.3 Cost of Quality: Poor vs. Good Quality
8.16.4 Cost of Quality: Not Only Failure Cost
8.16.5 COPQ: Internal Failure Costs
8.16.6 COPQ: External Failure Costs
8.16.7 Cost of Good Quality: Prevention Costs
8.16.8 Cost of Good Quality: Appraisal Costs
8.16.9 The Six Sigma Philosophy of Cost of Quality
8.16.10 Energy‐Efficiency Plan for Lean Manufacturing
8.16.11 Become ISO 50001 Ready
8.16.12 A Ten‐Step Outline for Energy Analysis: Understand the Energy Used to Transform Raw Material into Finished Product to Enhance Energy Efficiency (Stowe 2018)
8.17 Essential Roles of Industrial Environmental Managers
8.18 Goals of IEMs
8.19 Environmental Compliance and Compliance Assurances
8.20 Waste Reduction
8.20.1 Reuse and Recycling Processes
8.20.2 Benefits of Waste Minimization
8.20.3 Key Features: Industrial Environmental Management Process
Problems
References
9 Industrial Waste Minimization Methodology: Industrial Ecology, Eco‐Industrial Park and Manufacturing Process Intensification and Integration. 9.1 Introduction
9.2 Industrial Ecology
9.2.1 What Is EIP?
9.2.2 EIP Development
9.2.3 EIPs – The Ebara Process: Mini Case Study 9.1 in Japan
9.2.3.1 Advantages and Disadvantages
9.2.3.2 Cost Analysis
9.2.4 Mini‐Case Study 9.2: Seshasayee Paper and Board Ltd. in India
9.2.5 Mini‐Case Study 9.3: Materials and Energy Flow in an EIP in North Texas, USA
9.2.6 Mini‐Case Study 9.4: EIP Including Numerous Symbiotic Factories for Manufacturing Very Large Scale Photovoltaic System
9.3 Water–Energy Nexus
9.3.1 Technology Roadmaps and R&D
9.3.2 Circular Economy
9.3.2.1 Origins
9.3.2.2 Moving Away from the Linear Model
9.3.2.3 Emergence of the Idea
9.3.2.4 Sustainability
9.3.2.5 Use Waste as a Resource
9.3.2.6 Design for the Future
9.3.2.7 Preserve and Extend What's Already Made
9.3.2.8 Collaborate to Create Joint Value
9.3.2.9 Incorporate Digital Technology
9.3.3 Rethink the Business Model
9.3.3.1 Framework
9.3.3.2 Systems Thinking
9.3.4 Biomimicry
9.3.4.1 Cradle to Cradle
9.3.4.2 Toward the CE
9.3.4.3 Circular Business Models
9.4 CE Indicators in Relation to Eco‐Innovation
9.4.1 Development of the Concept of the CE
9.5 Process Intensification and Integration Potential in Manufacturing
9.5.1 What Is PI?
9.5.2 Case Study 9.5: Elimination of Dioxin and Furans by Alternative Chemical PI
9.5.3 Mini‐Case Study 9.2: Multi‐Pollutants Capture and Recovery of SOx, NOx, and Mercury in Coal‐Fired Power Plant. 9.5.3.1 Advanced Multi‐Pollutant Control: Intensified Regenerative Activated Coke Technology
9.5.3.2 AC and Regenerated Coke
9.5.3.3 Thermal Regeneration of AC
9.5.3.4 Performance and Benefits of ReACTTM
9.6 Manufacturing Process Integration
9.6.1 Process Integration Technique Has Few Possible Applications
9.7 New Sustainable Chemicals and Energy from Black Liquor Gasification Using Process Integration and Intensification
9.7.1 Introduction
9.7.2 Black Liquor Gasification (BLG): Introduction
9.7.2.1 Black Liquor Properties
9.7.2.2 BLG Technologies
9.8 Chemical Recovery and Power/Steam Cogeneration at Pulp and Paper Mills. 9.8.1 The Pulp and Paper Industry
9.8.2 Black Liquor Gasification Combined Cycle Power/Recovery
9.8.3 Biorefinery
9.8.4 Liquid Fuels Synthesis
9.8.5 Dimethyl Ether
9.8.6 Pressurized Chemrec BLG
9.8.7 Catalytic Hydrothermal Gasification of Black Liquor
9.8.8 Fischer–Tropsch Liquids
9.8.9 Mixed Alcohols
9.8.10 “WTW” Environmental Impact of Black Liquor Gasification
9.8.11 Water and Solid Waste
9.8.12 Mill‐Related Air Emissions
9.8.13 Tomlinson Boiler Air Emissions
9.8.14 Economic Development Opportunities
9.8.15 Cost‐Benefit Analysis
9.9 Conclusions
9.9.1 Summary
Problems
References
10 Quality Industrial Environmental Management: Sustainable Engineering in Manufacturing. 10.1 Introduction: Industry and the Global Environmental Issues
10.1.1 Industry Role and Trends
10.1.2 Code of Ethics for Engineers. 10.1.2.1 Engineers Play a Key Role in Manufacturing
Box 10.1 Corporate Sustainability
10.1.2.2 Sustainable Engineering
Sandestin Sustainable Engineering Principles
10.1.3 Sustainable Engineering Design Principles
Principles of Green Engineering
10.1.4 Design for Environmental Practices
10.1.5 Why Do Firms Want to Design for the Environment?
10.1.6 How Does a Business Design for the Environment?
10.1.7 Design for Environment
10.1.8 Design for Regulatory Compliance
10.1.9 Design for Testability
10.1.10 Design and Test for Service and Maintenance
10.1.11 Design for Manufacturing
10.1.12 Design for Assembly
10.1.13 Design for Disassembly
10.1.14 Design for Sustainable Manufacturing
10.1.15 Design for Sustainability
10.2 Integrating LCA in Sustainable Product Design and Development
10.3 Green Chemistry: The Twelve Principles of Green Chemistry
10.3.1 The Principles of Green Chemistry
10.4 The Hannover Principles. 10.4.1 Leadership in Energy and Environmental Design (LEED)
10.4.1.1 Certification Level
10.5 Sustainable Industries and Business
10.5.1 Eco‐Efficiency
10.5.2 Sustainable Supply Chain Systems
10.5.3 Sustainable Green Economy
10.6 Six Essential Characteristics
10.7 Social Services
10.8 Environmental Regulatory Law: Command and Control Market Based, and Reflexive
10.9 Business Ethics
10.9.1 The Two Traditional Issues Involved with Ethics
10.10 International Issues
10.11 Ethical Sustainability
10.12 Social Sustainability
10.13 Conclusions
10.13.1 Business
10.13.2 Corporate Sustainability
10.14 Strategy for Corporate Sustainability. 10.14.1 Business Case for Sustainability
10.14.2 Transparency
10.14.3 Stakeholder Engagement
Problems
References
Appendix A Conversion Factors
Appendix B International Environmental Law
Reference
Appendix C Air Pollutant Emission Factors: Stationary Point and Area Sources
Reference
Appendix D Frequently Asked Questions and Answers: Water Quality Model, Dispersion Model and Permits
D.1 Example Chain‐of‐Custody form for Use by POTWs
D.2 Water Quality Models
D.3 Frequently Asked Questions. Proposed General NPDES Permit for Industrial/Municipal Wastewaters Dischargers that Meet Objectives/Criteria at the Point of Discharge
D.4 Answers to Frequently Asked Questions. USEPA Prevention of Significant Deterioration Permit
D.5 Dispersion Model Development and Application
D.5.1 Model Development Is Based upon Several Assumptions
Gaussian or Normal Distribution
Observations
Point Source at Elevation H
Point Source at Elevation H with Reflection
Gaussian Dispersion Model
D.5.2 Information Required for Modeling the Dispersion of Emissions
D.5.3 Screening Modeling
D.5.4 AERSCREEN Examples
D.6 Hazardous Waste Manifest
References
Appendix E Industrial Hygiene Outlines
Reference
Appendix F Environmental Cost‐Benefit
Appendix G Resource Recovery: Waste‐To‐Energy Facility, City of Spokane, Washington, USA. G.1 Description of the Facility
G.1.1 Technology
Appendix H The Hannover Principles
Reference
Appendix I Environmental Goals and Business Goals Are Not Two Distinct Goal Sets
Appendix J Sample Codes of Ethics and Guidelines. J.1 National Society of Professional Engineers. J.1.1 Preamble
J.1.1.1 Fundamental Canons
J.1.1.2 Rules of Practice
J.1.1.3 Professional Obligations
Reference
Note
Index. a
b
c
d
e
f
g
h
i
k
l
m
n
o
p
q
r
s
t
u
v
w
z
WILEY END USER LICENSE AGREEMENT
Отрывок из книги
Tapas K. Das
Distinguished Speaker Award for 2007 given by the Development Organization for Sustainable Transformation (DOST), Indian Institute of Chemical Engineers. Dr. Das holds a BS in Chemical Engineering from Jadavpur University in Kolkata, India, and PhD from Bradford University, Bradford, England. Dr. Das was a postdoctoral fellow at London’s Imperial College of Science, Technology, and Medicine and a visiting scientist at Princeton University. He has wide practical and theoretical experience in various areas, including air toxics and aerosols, industrial wastewater treatment for water reuse, solid waste management and combustion, profitable process pollution prevention, reuse, recycle, redesign, sustainable engineering, and sustainability. Dr. Das is a registered professional engineer in the state of Washington. Dr. Das is the author of the book Toward Zero Discharge: Innovative Methodology and Technologies for Process Pollution Prevention (Wiley, 2005).
.....
An environmental impact statement (EIS), under US environmental law, is a document required by the National Environmental Policy Act (NEPA) for certain actions “significantly affecting the quality of the human environment” (NEPA 1969). An EIS is a tool for decision making. It describes the positive and negative environmental effects of a proposed action, and it usually also lists one or more alternative actions that may be chosen instead of the action described in the EIS. Several US state governments require that a document similar to an EIS be submitted to the state for certain actions.
The purpose of the NEPA is to promote informed decision making by federal agencies by making “detailed information concerning significant environmental impacts” available to both agency leaders and the public (Robertson v. Methow Valley Citizens Council 1989). The NEPA was the first piece of legislation that created a comprehensive method to assess potential and existing environmental risks at once. It also encourages communication and cooperation between all the actors involved in environmental decisions, including government officials, private businesses, and citizens (Felleman 2013).
.....