System Reliability Theory
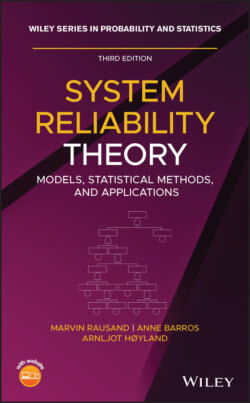
Реклама. ООО «ЛитРес», ИНН: 7719571260.
Оглавление
Marvin Rausand. System Reliability Theory
Table of Contents
List of Tables
List of Illustrations
Guide
Pages
Wiley Series in Probability and Statistics
System Reliability Theory. Models, Statistical Methods, and Applications
Preface
Main Changes from the Second Edition
Supplementary Information on the Internet
Intended Audience
Aims and Delimitation
Authors
Acknowledgments
References
About the Companion Website
Open Site
Instructor Site
GitHub Site
Contact Person
1 Introduction. 1.1 What is Reliability?
Definition 1.1 (Reliability)
1.1.1 Service Reliability
Definition 1.2 (Service reliability)
1.1.2 Past and Future Reliability
1.2 The Importance of Reliability
1.2.1 Related Applications
1.3 Basic Reliability Concepts
1.3.1 Reliability
Inherent and Actual Reliability
Definition 1.3 (Inherent reliability)
Definition 1.4 (Actual reliability)
Software Reliability
1.3.2 Maintainability and Maintenance
Definition 1.5 (Maintainability)
Definition 1.6 (Maintenance)
1.3.3 Availability
1.3.4 Quality
Definition 1.7 (Quality)
1.3.5 Dependability
Definition 1.8 (Dependability)
Remark 1.1 (Translating the word “dependability”)
1.3.6 Safety and Security
Definition 1.9 (Safety)
Definition 1.10 (Security)
Remark 1.2 (Natural threats)
1.3.7 RAM and RAMS
Remark 1.3 (Broad interpretation of reliability)
1.4 Reliability Metrics
1.4.1 Reliability Metrics for a Technical Item
Example 1.1 (Average availability and downtime)
1.4.2 Reliability Metrics for a Service
Example 1.2 (Airline reliability and availability)
1.5 Approaches to Reliability Analysis
1.5.1 The Physical Approach to Reliability
1.5.2 Systems Approach to Reliability
System Models
1.6 Reliability Engineering
1.6.1 Roles of the Reliability Engineer
Roles in Design and Development
Roles in Normal Operation
1.6.2 Timing of Reliability Studies
1.7 Objectives, Scope, and Delimitations of the Book
1.8 Trends and Challenges
1.9 Standards and Guidelines
1.10 History of System Reliability
1930s
1940s
1950s
1960s
1970s
1980s
After 1990
1.11 Problems
References
Notes
2 The Study Object and its Functions. 2.1 Introduction
2.2 System and System Elements
Definition 2.1 (System)
2.2.1 Item
Definition 2.2 (Item)
2.2.2 Embedded Item
2.3 Boundary Conditions
Definition 2.3 (System boundary)
2.3.1 Closed and Open Systems
Definition 2.4 (Closed system)
Definition 2.5 (Open system)
2.4 Operating Context
Definition 2.6 (Operating context)
2.5 Functions and Performance Requirements
2.5.1 Functions
Example 2.1 (Flashlight)
Definition 2.7 (Function)
2.5.2 Performance Requirements
Definition 2.8 (Requirement)
2.5.3 Classification of Functions
2.5.4 Functional Modeling and Analysis
2.5.5 Function Trees
2.5.6 SADT and IDEF 0
2.6 System Analysis
2.6.1 Synthesis
2.7 Simple, Complicated, and Complex Systems
Remark 2.1 (Classical methods waste of time?)
2.8 System Structure Modeling
2.8.1 Reliability Block Diagram
System Structure
Boolean Representation
2.8.2 Series Structure
2.8.3 Parallel Structure
2.8.4 Redundancy
Definition 2.9 (Redundancy)
2.8.5 Voted Structure
2.8.6 Standby Structure
2.8.7 More Complicated Structures
Remark 2.2 (Series–parallel structures)
2.8.8 Two Different System Functions
Example 2.2 (Pipeline with safety valves)
Remark 2.3 (Terminology problem)
2.8.9 Practical Construction of RBDs
2.9 Problems
References
Notes
Chapter 3 Failures and Faults. 3.1 Introduction
3.1.1 States and Transitions
Example 3.1 (Safety valve)
Remark 3.1 (States and transition)
3.1.2 Operational Modes
3.2 Failures
Definition 3.1 (Failure of an item)
Example 3.2 (Car tires)
3.2.1 Failures in a State
Example 3.3 (Water pump)
Example 3.4 (Light bulb–continuously “on”)
Example 3.5 (Light bulb–“on” only on demand)
3.2.2 Failures During Transition
Example 3.6 (Lawn mower)
Example 3.7 (Safety valve)
3.3 Faults
Definition 3.2 (Fault of an item)
3.4 Failure Modes
Definition 3.3 (Failure mode)
Example 3.8 (Failure modes of a sink faucet)
Example 3.9 (Electric doorbell)
3.5 Failure Causes and Effects
3.5.1 Failure Causes
Definition 3.4 (Failure cause)
3.5.2 Proximate Causes and Root Causes
Definition 3.5 (Proximate cause)
Example 3.10 (Flashlight)
Definition 3.6 (Root cause)
3.5.3 Hierarchy of Causes
3.6 Classification of Failures and Failure Modes
3.6.1 Classification According to Local Consequence
3.6.2 Classification According to Cause
Primary Failures
Secondary Failures
Systematic Failures
Example 3.11 (Airbag system in a car)
Example 3.12 (Failure causes of a gas detection system)
Security Failures
Additional Types of Failures
Remark 3.2 (Functionally unavailable)
Failures Named According to the Cause of Failure
3.6.3 Failure Mechanisms
3.6.4 Software Faults
Definition 3.7 (Software fault/bug)
3.6.5 Failure Effects
Example 3.13 (Failure effects of brake pad failure)
3.7 Failure/Fault Analysis
3.7.1 Cause and Effect Analysis
Example 3.14 (Car will not start)
3.7.2 Root Cause Analysis
Definition 3.8 (Root cause analysis)
Example 3.15 (Car will not start)
3.8 Problems
References
Chapter 4 Qualitative System Reliability Analysis. 4.1 Introduction
4.1.1 Deductive Versus Inductive Analysis
4.2 FMEA/FMECA
4.2.1 Types of FMECA
Additional Variants of FMECA
Hardware Versus Functional Approach
4.2.2 Objectives of FMECA
4.2.3 FMECA Procedure
Risk Priority Number
4.2.4 Applications
4.3 Fault Tree Analysis
4.3.1 Fault Tree Symbols and Elements
Remark 4.2 (Terminology)
4.3.2 Definition of the Problem and the Boundary Conditions
4.3.3 Constructing the Fault Tree
Rules for Fault Tree Construction
Example 4.1 (Fire detector system)
Remark 4.3 (The fault tree is not unique)
4.3.4 Identification of Minimal Cut and Path Sets
Definition 4.1 (Minimal cut set in fault tree)
4.3.5 MOCUS
Definition 4.2 (Minimal path set in fault tree)
4.3.6 Qualitative Evaluation of the Fault Tree
Example 4.2 (Offshore separator)
4.3.7 Dynamic Fault Trees
4.4 Event Tree Analysis
4.4.1 Initiating Event
4.4.2 Safety Functions
4.4.3 Event Tree Construction
4.4.4 Description of Resulting Event Sequences
Example 4.3 (Offshore separator–event tree)
4.5 Fault Trees versus Reliability Block Diagrams
Remark 4.4 (Terminology)
Example 4.4 (Example 4.1 (cont.))
4.5.1 Recommendation
4.6 Structure Function
4.6.1 Series Structure
4.6.2 Parallel Structure
Boolean Algebra
4.6.3 oo:G Structure
Voted Structures in Safety Systems
4.6.4 Truth Tables
4.7 System Structure Analysis
4.7.1 Single Points of Failure
Definition 4.3 (Single point of failure)
4.7.2 Coherent Structures
Remark 4.5 (Relevant and irrelevant components)
Definition 4.4 (Coherent structure)
4.7.3 General Properties of Coherent Structures
Property 4.1
Property 4.2
Property 4.3
4.7.4 Structures Represented by Paths and Cuts
Definition 4.5 (Minimal path set)
Definition 4.6 (Minimal cut set)
Example 4.5
Example 4.6 (Bridge structure)
Example 4.7 (2oo3 structure)
Example 4.8 (Example 4.7 (cont.))
Example 4.9 (Example 4.8 (cont.))
4.7.5 Pivotal Decomposition
Example 4.10 (Bridge structure)
4.7.6 Modules of Coherent Structures
Definition 4.7 (Coherent module – 1)
Definition 4.8 (Coherent module – 2)
Definition 4.9 (Modular decomposition)
4.8 Bayesian Networks
4.8.1 Illustrative Examples
Example 4.11 (BN for a series structure)
Example 4.12 (BN for a parallel structure)
Example 4.13 (2oo3 structure)
Probabilistic Evaluation
4.9 Problems
References
Notes
5 Probability Distributions in Reliability Analysis
5.1 Introduction
5.1.1 State Variable
5.1.2 Time‐to‐Failure
5.2 A Dataset
5.2.1 Relative Frequency Distribution
5.2.2 Empirical Distribution and Survivor Function
5.3 General Characteristics of Time‐to‐Failure Distributions
5.3.1 Survivor Function
5.3.2 Failure Rate Function
Remark 5.1 (The difference between f(t) and z(t))
Remark 5.2 (The failure rate function versus ROCOF)
The Bathtub Curve
Cumulative Failure Rate
Average Failure Rate
A Property of
5.3.3 Conditional Survivor Function
5.3.4 Mean Time‐to‐Failure
Law of Large Numbers
Remark 5.3 (MTTF derived by Laplace transform)
5.3.5 Additional Probability Metrics
Variance
Moments
Percentile Function
Median Lifetime
Mode
Example 5.1
5.3.6 Mean Residual Lifetime
Remark 5.4 (Remaining useful lifetime)
Example 5.2 (Mean residual lifetime)
5.3.7 Mixture of Time‐to‐Failure Distributions
5.4 Some Time‐to‐Failure Distributions
5.4.1 The Exponential Distribution
Survivor Function
MTTF
Failure Rate Function
Median Time‐to‐Failure
Changed Time Scale
Probability of Failure in a Short Time Interval
Series Structure of Independent Components
Conditional Survivor Function and Mean Residual Lifetime
The Difference Between a Random Variable and a Parameter
Example 5.3 (Rotary pump)
Example 5.4 (Probability of one item failing before the other)
Mixture of Exponential Distributions
Stepwise Constant Failure Rate
5.4.2 The Gamma Distribution
Special Cases
The Distribution
Example 5.5 (Mixture of exponential distributions)
Remark 5.5 (Mixed distributions)
5.4.3 The Weibull Distribution
Two‐Parameter Weibull Distribution
Remark 5.6 (Choice of parameters)
Survivor Function
Failure Rate Function
Remark 5.7 (A warning)
MTTF
Example 5.6 (Choke valve)
Series Structure of Independent Components
Identical Components
Example 5.7 (Numerical example)
Three‐Parameter Weibull Distribution
5.4.4 The Normal Distribution
Survivor Function
Failure Rate Function
Example 5.8 (Wear‐out of car tires)
5.4.5 The Lognormal Distribution
Survivor Function
Failure Rate Function
Repair Time Distribution
Median and Error Factor
Uncertainty in Failure Rate Estimate
Example 5.9 (Fatigue analysis)
5.4.6 Additional Time‐to‐Failure Distributions
5.5 Extreme Value Distributions
5.5.1 The Gumbel Distribution of the Smallest Extreme
5.5.2 The Gumbel Distribution of the Largest Extreme
5.5.3 The Weibull Distribution of the Smallest Extreme
Example 5.10 (Pitting corrosion)
5.6 Time‐to‐Failure Models With Covariates
Example 5.11 (Covariates for a shutdown valve)
5.6.1 Accelerated Failure Time Models
Example 5.12 (Constant failure rate)
5.6.2 The Arrhenius Model
The Arrhenius Model for Times‐to‐Failure
Example 5.13 (Constant failure rate)
Example 5.14 (Weibull distribution)
5.6.3 Proportional Hazards Models
5.7 Additional Continuous Distributions
5.7.1 The Uniform Distribution
5.7.2 The Beta Distribution
5.8 Discrete Distributions
5.8.1 Binomial Situation
5.8.2 The Binomial Distribution
5.8.3 The Geometric Distribution
5.8.4 The Negative Binomial Distribution
Remark 5.8 (The name of the distribution)
5.8.5 The Homogeneous Poisson Process
Example 5.15 (Repairable item)
5.9 Classes of Time‐to‐Failure Distributions
5.9.1 IFR and DFR Distributions
Example 5.16 (The uniform distribution over )
Example 5.17 (The exponential distribution)
Example 5.18 (The Weibull distribution)
Example 5.19 (The gamma distribution)
5.9.2 IFRA and DFRA Distributions
5.9.3 NBU and NWU Distributions
5.9.4 NBUE and NWUE Distributions
Definition 5.1 (New better/worse than used in expectation)
5.9.5 Some Implications
5.10 Summary of Time‐to‐Failure Distributions
5.11 Problems
References
Notes
6 System Reliability Analysis
6.1 Introduction
6.1.1 Assumptions
6.2 System Reliability
6.2.1 Reliability of Series Structures
Example 6.1 (Series structure)
6.2.2 Reliability of Parallel Structures
Example 6.2 (Parallel structure)
6.2.3 Reliability of oo Structures
Example 6.3 (2oo3 structure)
Example 6.4 (Alarm system for gas leakage)
6.2.4 Pivotal Decomposition
Law of Total Probability
6.2.5 Critical Component
6.3 Nonrepairable Systems
6.3.1 Nonrepairable Series Structures
Example 6.5 (Series structure with constant failure rates)
Example 6.6 (Series structure with Weibull‐distributed times‐to‐failure)
Example 6.7 (Bathtub curve obtained by three Weibull distributions)
6.3.2 Nonrepairable Parallel Structures
Parallel Structure of Identical Components
Remark 6.1 (An alternative derivation)
Example 6.8 (Parallel structure of two identical components)
Example 6.9 (Parallel structure of two different components)
Example 6.10 (Parallel structure of Weibull‐distributed components)
6.3.3 Nonrepairable 2oo3 Structures
6.3.4 A Brief Comparison
6.3.5 Nonrepairable oo Structures
6.4 Standby Redundancy
6.4.1 Passive Redundancy, Perfect Switching, No Repairs
Central Limit Theorem
6.4.2 Cold Standby, Imperfect Switch, No Repairs
Example 6.11 (Standby pump)
6.4.3 Partly Loaded Redundancy, Imperfect Switch, No Repairs
6.5 Single Repairable Items
6.5.1 Availability
Definition 6.1 (Availability)
Definition 6.2 (Unavailability)
Definition 6.3 (Interval availability)
Definition 6.4 (Average availability)
Example 6.12 (Average availability)
Definition 6.5 (Limiting availability)
6.5.2 Average Availability with Perfect Repair
Example 6.13 (Average availability with perfect repair)
Remark 6.2 (MTTF versus MUT)
6.5.3 Availability of a Single Item with Constant Failure and Repair Rates
6.5.4 Operational Availability
6.5.5 Production Availability
6.5.6 Punctuality
6.5.7 Failure Rate of Repairable Items
Failure Rate Function
ROCOF
Approximation Formula for ROCOF
Example 6.14 (Constant failure and repair rates)
Vesely's Failure Rate
Example 6.15 (Constant failure and repair rates – cont.)
6.6 Availability of Repairable Systems
Example 6.16 (System availability calculation)
6.6.1 The MUT and MDT of Repairable Systems
Remark 6.3 (Birnbaum's metric of importance)
Example 6.17 (Repairable series systems)
A Numerical Example
Example 6.18 (Repairable parallel systems)
A Numerical Example
Remark 6.4 (Assumptions and limitations)
6.6.2 Computation Based on Minimal Cut Sets
Example 6.19 (Repairable 2oo3 structure)
A Numerical Example
Remark 6.5 (Not fully correct result)
6.6.3 Uptimes and Downtimes for Reparable Systems
Example 6.20 (Parallel structure of three components)
A Numerical Example
6.7 Quantitative Fault Tree Analysis
6.7.1 Terminology and Symbols
6.7.2 Delimitations and Assumptions
Remark 6.6 (Basic events are states)
6.7.3 Fault Trees with a Single AND‐Gate
6.7.4 Fault Tree with a Single OR‐Gate
6.7.5 The Upper Bound Approximation Formula for
Remark 6.7 (Rare event approximation)
6.7.6 The Inclusion–Exclusion Principle
Example 6.21 (Bridge structure)
Approximation Formulas by the Inclusion–Exclusion Principle
Example 6.22 (Bridge structure – cont.)
6.7.7 ROCOF of a Minimal Cut Parallel Structure
6.7.8 Frequency of the TOP Event
Example 6.23 (Bridge structure)
Kinetic Tree Theory
6.7.9 Binary Decision Diagrams
Example 6.24 (BDD deduced from a truth table)
6.8 Event Tree Analysis
6.9 Bayesian Networks
6.9.1 Influence and Cause
6.9.2 Independence Assumptions
6.9.3 Conditional Probability Table
6.9.4 Conditional Independence
Conditional Independence
Example 6.25 (System of two pumps)
6.9.5 Inference and Learning
6.9.6 BN and Fault Tree Analysis
6.10 Monte Carlo Simulation
6.10.1 Random Number Generation
Generation of Random Variables with a Specified Distribution
Simulating the Lifespan of a Repairable Component
6.10.2 Monte Carlo Next Event Simulation
Single Item with Only One Failure Mode
6.10.3 Simulation of Multicomponent Systems
Example 6.26 (Production availability simulation)
6.11 Problems
References
Note
7 Reliability Importance Metrics. 7.1 Introduction
7.1.1 Objectives of Reliability Importance Metrics
7.1.2 Reliability Importance Metrics Considered
7.1.3 Assumptions and Notation
Remark 7.1 (An advice to the reader)
7.2 Critical Components
Definition 7.1 (Critical component / basic event)
Example 7.1 (Critical component)
7.3 Birnbaum's Metric for Structural Importance
Definition 7.2 (Birnbaum's metric for structural importance)
Example 7.2 (Birnbaum's metric for structural importance)
7.4 Birnbaum's Metric of Reliability Importance
Definition 7.3 (Birnbaum's metric of reliability importance ‐ 1)
Example 7.3 (Series structure)
Example 7.4 (Parallel structure)
7.4.1 Birnbaum's Metric in Fault Tree Analysis
Example 7.5 (Fault tree with a single AND‐gate)
Example 7.6 (Fault tree with a single OR‐gate)
7.4.2 A Second Definition of Birnbaum's Metric
Remark 7.2 (Straight line)
Definition 7.4 (Birnbaum's metric of importance ‐ 2)
Example 7.7 (Series structure)
Example 7.8 (Parallel structure)
7.4.3 A Third Definition of Birnbaum's Metric
Definition 7.5 (Birnbaum's metric of importance – 3)
Example 7.9 (Series structure)
Example 7.10 (Parallel structure)
7.4.4 Computation of Birnbaum's Metric for Structural Importance
7.4.5 Variants of Birnbaum's Metric
7.5 Improvement Potential
Definition 7.6 (Improvement potential)
7.5.1 Relation to Birnbaum's Metric
7.5.2 A Variant of the Improvement Potential
7.6 Criticality Importance
Definition 7.7 (Criticality importance – 1)
Definition 7.8 (Criticality importance – 2)
7.7 Fussell–Vesely's Metric
Definition 7.9 (Fussell–Vesely's metric – 1)
7.7.1 Derivation of Formulas for Fussell–Vesely's Metric
Example 7.11 (Bridge structure)
7.7.2 Relationship to Other Metrics for Importance
Definition 7.10 (Fussell–Vesely's metric – 2)
Remark 7.3
Example 7.12 (Example 7.11 cont.)
7.8 Differential Importance Metric
Definition 7.11 (Differential importance metric)
7.8.1 Option 1
7.8.2 Option 2
Example 7.13 (Simple structure)
7.9 Importance Metrics for Safety Features
7.9.1 Risk Achievement Worth
Definition 7.12 (Risk achievement worth)
Example 7.14 (A numerical example)
Example 7.15 (Barrier against demands)
7.9.2 Risk Reduction Worth
Definition 7.13 (Risk reduction worth)
Example 7.16 (A numerical example)
7.9.3 Relationship with the Improvement Potential
Example 7.17
Remark 7.4
7.10 Barlow–Proschan's Metric
Definition 7.14 (Barlow–Proschan's metric for a nonrepairable component)
Definition 7.15 (Barlow–Proschan's metric for a repairable component)
Example 7.18 (Series structure)
Example 7.19 (Parallel structure)
7.11 Problems
References
Notes
8 Dependent Failures. 8.1 Introduction
8.1.1 Dependent Events and Variables
Remark 8.1 (Mutually exclusive versus independent)
8.1.2 Correlated Variables
Remark 8.2 (Dependence versus interdependence)
8.2 Types of Dependence
8.3 Cascading Failures
Definition 8.1 (Cascading failure)
Example 8.1 (Fukushima nuclear disaster)
8.3.1 Tight Coupling
8.4 Common‐Cause Failures
Definition 8.2 (Common‐cause failure)
Remark 8.3 (Increased stress)
8.4.1 Multiple Failures that Are Not a CCF
Definition 8.3 (Multiple failure with a shared cause, MFSC)
8.4.2 Causes of CCF
Definition 8.4 (Common‐cause component group, CCCG)
8.4.3 Defenses Against CCF
Remark 8.4 (Condition monitoring and software)
8.5 CCF Models and Analysis
8.5.1 Explicit Modeling
8.5.2 Implicit Modeling
8.5.3 Modeling Approach
8.5.4 Model Assumptions
8.6 Basic Parameter Model
8.6.1 Probability of a Specific Multiplicity
8.6.2 Conditional Probability of a Specific Multiplicity
8.7 Beta‐Factor Model
Example 8.2 (Interpretation of the beta‐factor)
8.7.1 Relation to the BPM
Remark 8.5 (Unreliable components have higher beta‐factor)
8.7.2 Beta‐Factor Model in System Analysis
Example 8.3 (Parallel structure of two identical components)
Example 8.4 (2oo3:G structure of identical components)
Example 8.5 (Series structure of identical components)
8.7.3 Beta‐Factor Model for Nonidentical Components
Arithmetic Versus Geometric Average
Example 8.6 (Parallel structure of nonidentical components)
Example 8.7 (Beta‐factor with very different failure rates)
Example 8.8 (2oo3:G voted group with different failure rates)
8.7.4 ‐Factor Model
8.8 Multi‐parameter Models
8.8.1 Binomial Failure Rate Model
Example 8.9 (2oo3:G structure of identical components)
8.8.2 Multiple Greek Letter Model
System with Three Identical Components
8.8.3 Alpha‐Factor Model
Structure with Three Identical Components
8.8.4 Multiple Beta‐Factor Model
8.9 Problems
References
Notes
9 Maintenance and Maintenance Strategies. 9.1 Introduction
9.1.1 What is Maintenance?
9.2 Maintainability
Example 9.1 (Subsea oil/gas production system)
9.3 Maintenance Categories
An alternative classification of maintenance
Example 9.2 (Automobile service)
Example 9.3 (Proof test)
Remark 9.1 (Modification)
9.3.1 Completeness of a Repair Task
9.3.2 Condition Monitoring
Definition 9.1 (Condition monitoring)
9.4 Maintenance Downtime
9.4.1 Downtime Caused by Failures
Exponential Distribution
Example 9.4 (Exponentially distributed downtime)
Normal Distribution
Lognormal Distribution
9.4.2 Downtime of a Series Structure
Example 9.5 (Item with independent failure modes)
9.4.3 Downtime of a Parallel Structure
9.4.4 Downtime of a General Structure
9.5 Reliability Centered Maintenance
Definition 9.2 (Reliability‐centered maintenance, RCM)
9.5.1 What is RCM?
9.5.2 Main Steps of an RCM Analysis
Step 1: Study Preparation
Step 2: System Selection and Definition
Step 3: Functional Failure Analysis
Step 3(i): Identification of System Functions
Step 3(ii): Identification of Interfaces
Step 3(iii): Functional Failures
Step 4: Critical Item Selection
Step 5: Data Collection and Analysis
Step 6: Failure Modes, Effects, and Criticality Analysis
Step 7: Selection of Maintenance Task
Step 8: Determination of Maintenance Intervals
Step 9: Preventive Maintenance Comparison Analysis
Step 10: Treatment of Non‐MSIs
Step 11: Implementation
Step 12: In‐service Data Collection and Updating
9.6 Total Productive Maintenance
9.7 Problems
References
Note
10 Counting Processes. 10.1 Introduction
10.1.1 Counting Processes
Definition 10.1 (Counting process)
Example 10.1 (Sad versus happy items)
Example 10.2 (Compressor failure data)
10.1.2 Basic Concepts
Definition 10.2 (Lattice distribution)
10.1.3 Martingale Theory
10.1.4 Four Types of Counting Processes
10.2 Homogeneous Poisson Processes
Definition 10.3 (Homogeneous Poisson process – 1)
Definition 10.4 (Homogeneous Poisson process – 2)
Definition 10.5 (Homogeneous Poisson process – 3)
10.2.1 Main Features of the HPP
Remark 10.1 (Comparing definitions of the HPP)
10.2.2 Asymptotic Properties
10.2.3 Estimate and Confidence Interval
10.2.4 Sum and Decomposition of HPPs
Example 10.3 (Failures of a specific type)
10.2.5 Conditional Distribution of Failure Time
10.2.6 Compound HPPs
Wald's equation
Example 10.4 (Exponentially distributed consequences)
10.3 Renewal Processes
Example 10.5 (A renewal process)
10.3.1 Basic Concepts
10.3.2 The Distribution of
Example 10.6 (IFR interoccurrence times)
10.3.3 The Distribution of
10.3.4 The Renewal Function
10.3.5 The Renewal Density
Example 10.7 (Gamma distributed renewal periods)
Example 10.8 (Weibull distributed renewal periods)
10.3.6 Age and Remaining Lifetime
Limiting Distribution
Example 10.9 (Example 10.7 (cont.))
Lemma 10.1
10.3.7 Bounds for the Renewal Function
Example 10.11 (Example 10.5 (cont.))
10.3.8 Superimposed Renewal Processes
Example 10.12 (Series structure)
10.3.9 Renewal Reward Processes
10.3.10 Delayed Renewal Processes
The Distribution of
The Distribution of
The Renewal Function
The Renewal Density
Definition 10.6 (Stationary renewal process)
Remark 10.4
10.3.11 Alternating Renewal Processes
Availability
Example 10.15 (Parallel structure)
Mean Number of Failures/Repairs
Availability at a Given Point of Time
Example 10.16 (Exponential time‐to‐failure and exponential downtime)
Example 10.17 (Exponential time‐to‐failure and constant downtime)
10.4 Nonhomogeneous Poisson Processes
10.4.1 Introduction and Definitions
Definition 10.7 (Nonhomogeneous Poisson process)
10.4.2 Some Results
Time to First Failure
Time Between Failures
Example 10.18
Relation to the Homogeneous Poisson Process
10.4.3 Parametric NHPP Models
The Power Law Model
The Linear Model
The Log‐Linear Model
10.4.4 Statistical Tests of Trend
The Laplace Test
Military Handbook Test
10.5 Imperfect Repair Processes
10.5.1 Brown and Proschan's model
10.5.2 Failure Rate Reduction Models
10.5.3 Age Reduction Models
10.5.4 Trend Renewal Process
10.6 Model Selection
10.7 Problems
References
Notes
11 Markov Analysis. 11.1 Introduction
Example 11.1 (States of a parallel structure)
11.1.1 Markov Property
Definition 11.1 (Markov property)
11.2 Markov Processes
11.2.1 Procedure to Establish the Transition Rate Matrix
Example 11.2 (Parallel structure – cont.)
Example 11.3 (Parallel structure – cont.)
Example 11.4 (Homogeneous Poisson process)
11.2.2 Chapman–Kolmogorov Equations
11.2.3 Kolmogorov Differential Equations
11.2.4 State Equations
Remark 11.1 (An alternative way of writing the state equations)
Example 11.5 (Single component)
11.3 Asymptotic Solution
Remark 11.2 (Numerical solution with R)
Example 11.6 (Power station with two generators)
11.3.1 System Performance Metrics
Visit Frequency
Mean Duration of a Visit
System Availability
Frequency of System Failures
Mean Duration of a System Failure
Mean Time Between System Failures
Mean Functioning Time Until System Failure
11.4 Parallel and Series Structures
11.4.1 Parallel Structures of Independent Components
Mean Duration of the Visits
Visit Frequency
11.4.2 Series Structures of Independent Components
11.4.3 Series Structure of Components Where Failure of One Component Prevents Failure of the Other
11.5 Mean Time to First System Failure
11.5.1 Absorbing States
Example 11.7 (Parallel structure of two independent components)
11.5.2 Survivor Function
11.5.3 Mean Time to the First System Failure
Example 11.8 (Example 11.7 (Cont.))
Procedure for Finding MTTFS
Example 11.9 (Parallel structure of two independent components)
Some Special Cases
11.6 Systems with Dependent Components
11.6.1 Common Cause Failures
11.6.2 Load‐Sharing Systems
Example 11.10 (System of two generators)
11.7 Standby Systems
11.7.1 Parallel System with Cold Standby and Perfect Switching
11.7.2 Parallel System with Cold Standby and Perfect Switching (Item is the Main Operating Item)
11.7.3 Parallel System with Cold Standby and Imperfect Switching (Item is the Main Operating Item)
11.7.4 Parallel System with Partly Loaded Standby and Perfect Switching (Item is the Main Operating Item)
11.8 Markov Analysis in Fault Tree Analysis
11.8.1 Cut Set Information
11.8.2 System Information
11.9 Time‐Dependent Solution
11.9.1 Laplace Transforms
11.10 Semi‐Markov Processes
Definition 11.2 (Semi‐Markov process)
11.11 Multiphase Markov Processes
Definition 11.3 (Multiphase Markov process)
11.11.1 Changing the Transition Rates
11.11.2 Changing the Initial State
11.12 Piecewise Deterministic Markov Processes
11.12.1 Definition of PDMP
Definition 11.4 (Piecewise deterministic Markov process)
11.12.2 State Probabilities
11.12.3 A Specific Case
Discrete States
Continuous States
State Probabilities
Numerical Scheme
11.13 Simulation of a Markov Process
Remark 11.3 (Accuracy)
Example 11.12 (Simulating a Markov process)
Remark 11.4 (Markov analysis with R)
11.14 Problems
References
Notes
12 Preventive Maintenance. 12.1 Introduction
Definition 12.1 (Preventive maintenance)
12.2 Terminology and Cost Function
12.3 Time‐Based Preventive Maintenance
12.3.1 Age Replacement
Example 12.1 (Age replacement–Weibull distribution)
Time Between Failures
Age Replacement – Availability Criterion
12.3.2 Block Replacement
Example 12.2 (Block replacement)
Block Replacement with Minimal Repair
Block Replacement with Limited Number of Spares
Example 12.3 (Block replacement without spare item)
Example 12.4 (Block replacement with limited number of spare items)
12.3.3 – Intervals
Example 12.5 (Cracks in railway rails)
Deterministic – Interval and Repair Time and Perfect Inspection
Remark 12.1
Stochastic – Interval, Deterministic Repair Time, and Nonperfect Inspection
Delay Time Models
12.4 Degradation Models
12.4.1 Remaining Useful Lifetime
Remark 12.2 (Another interpretation of RUL)
Data‐Driven Prognostics with no Probabilistic Modeling
Data‐Driven Prognostics with Probabilistic Modeling
12.4.2 Trend Models; Regression‐Based Models
Wiener Process with Linear Drift
The Distribution of
12.4.3 Models with Increments
Example 12.6 (Exponentially distributed increments)
Levy Process
Homogeneous Gamma Process
The Distribution of
12.4.4 Shock Models
The Distribution of
12.4.5 Stochastic Processes with Discrete States
12.4.6 Failure Rate Models
12.5 Condition‐Based Maintenance
12.5.1 CBM Strategy
12.5.2 Continuous Monitoring and Finite Discrete State Space
Maintenance Strategies
Example 12.7 (Degradation and maintenance of multicomponent systems)
Example 12.8 (Degradation and maintenance of bridges)
Maintenance Cost
12.5.3 Continuous Monitoring and Continuous State Space
Maintenance Strategy
Maintenance Cost
12.5.4 Inspection‐Based Monitoring and Finite Discrete State Space
Time‐Based Inspections Versus Condition‐Based Inspections
Maintenance Strategy
Maintenance Cost
12.5.5 Inspection‐Based Monitoring and Continuous State Space
Maintenance/Inspection Strategy
Maintenance Cost
12.6 Maintenance of Multi‐Item Systems
12.6.1 System Model
Models for the System Structure
Stochastic Models for Single Items
Interactions Between Items
12.6.2 Maintenance Models
Opportunistic Maintenance and Grouping
Definition 12.2 (Opportunistic maintenance)
Condition‐Based Maintenance
12.6.3 An Illustrative Example
Degradation Model for Items of Type
CBM Strategy
Maintenance Cost
12.7 Problems
References
Notes
Chapter 13 Reliability of Safety Systems. 13.1 Introduction
13.2 Safety‐Instrumented Systems
13.2.1 Main SIS Functions
Example 13.1 (Safety systems on offshore oil and gas platforms)
13.2.2 Testing of SIS Functions
Diagnostic Self‐Testing
Proof Testing
13.2.3 Failure Classification
Example 13.2 (Safety shutdown valve)
13.3 Probability of Failure on Demand
13.3.1 Probability of Failure on Demand
Example 13.3 (Single item)
Example 13.4 (Parallel structure)
Remark 13.1 (The average of a product is not the product of the averages)
Example 13.5 (2oo3 structure)
Example 13.6 (Series structure)
13.3.2 Approximation Formulas
13.3.3 Mean Downtime in a Test Interval
Example 13.7 (Example 13.3 (Cont.))
Example 13.8 (Example 13.4 (Cont.))
13.3.4 Mean Number of Test Intervals Until First Failure
Example 13.9
13.3.5 Staggered Testing
13.3.6 Nonnegligible Repair Time
Example 13.10 (Downhole safety valve)
13.4 Safety Unavailability
13.4.1 Probability of Critical Situation
13.4.2 Spurious Trips
Example 13.11 (Parallel structure)
Example 13.12 (2oo3:G structure)
13.4.3 Failures Detected by Diagnostic Self‐Testing
Example 13.13 (Process shutdown valve)
13.5 Common Cause Failures
Example 13.14 (Pressure sensors CCF)
13.5.1 Diagnostic Self‐Testing and CCFs
Remark 13.2
Example 13.15 (Parallel structure)
Example 13.16 (2oo3 structure)
Remark 13.3
13.6 CCFs Between Groups and Subsystems
13.6.1 CCFs Between Voted Groups
13.6.2 CCFs Between Subsystems
13.7 IEC 61508
13.7.1 Safety Lifecycle
13.7.2 Safety Integrity Level
Definition 13.1 (Safety integrity)
13.7.3 Compliance with IEC 61508
13.8 The PDS Method
13.9 Markov Approach
Example 13.17 (Safety valve)
13.9.1 All Failures are Repaired After Each Test
13.9.2 All Critical Failures Are Repaired after Each Test
13.9.3 Imperfect Repair after Each Test
13.10 Problems
References
Notes
14 Reliability Data Analysis. 14.1 Introduction
14.1.1 Purpose of the Chapter
14.2 Some Basic Concepts
14.2.1 Datasets
14.2.2 Survival Times
Entering Survival Times into R
The Survival R Package
14.2.3 Categories of Censored Datasets
Censoring of Type I
Censoring of Type II
Censoring of Type III
Censoring of Type IV
Right Censoring
Example 14.1 (Censoring caused by other failures)
Informative Censoring
14.2.4 Field Data Collection Exercises
14.2.5 At‐Risk‐Set
14.3 Exploratory Data Analysis
14.3.1 A Complete Dataset
Remark 14.1 (An advise)
Ties
14.3.2 Sample Metrics
Mean
Median
Variance and Standard Deviation
Quantiles
Quartiles
Interquartile Range
Sample Moments and Central Moments
Skewness
Kurtosis
14.3.3 Histogram
14.3.4 Density Plot
14.3.5 Empirical Survivor Function
14.3.6 Q–Q Plot
14.4 Parameter Estimation
14.4.1 Estimators and Estimates
14.4.2 Properties of Estimators
Unbiased
Small Variance
Mean Squared Error
Consistency
Chebyshev's Inequality
Example 14.2 (Binomial model)
Remark 14.2 (Confusing symbols)
14.4.3 Method of Moments Estimation
Example 14.3 (Exponential distribution)
Example 14.4 (Gamma distribution)
General Properties of the MME
14.4.4 Maximum Likelihood Estimation
Likelihood Function
Remark 14.3 (The likelihood function is not a probability distribution)
Maximum Likelihood Estimate
Definition 14.1 (Maximum likelihood estimate, MLE)
Example 14.5 (Binomial distribution)
Example 14.6 (Homogeneous Poisson Process)
Example 14.7 (Exponential distribution)
Remark 14.4 (Factors not depending on the parameter can be deleted)
General Properties of the MLE
MLE with R
Likelihood Function for Censored Datasets
14.4.5 Exponentially Distributed Lifetimes
Exponentially Distribution: Complete Sample
Example 14.8 (Exponential distribution, complete sample)
Total‐Time‐on‐Test
Exponentially Distribution: Censored Data
Censoring of Type II
Censoring of Type I
14.4.6 Weibull Distributed Lifetimes
Complete Sample
Weibull Analysis with R
Censoring of Type II
14.5 The Kaplan–Meier Estimate
14.5.1 Motivation for the Kaplan–Meier Estimate Based a Complete Dataset
14.5.2 The Kaplan–Meier Estimator for a Censored Dataset
Example 14.9 (Kaplan–Meier estimate)
Kaplan–Meier Estimate with R
Some Properties of the Kaplan–Meier Estimator
14.6 Cumulative Failure Rate Plots
Example 14.10 (Exponential distribution)
Example 14.11 (Weibull distribution)
14.6.1 The Nelson–Aalen Estimate of the Cumulative Failure Rate
Example 14.12 (Nelson–Aalen estimate for a censored dataset)
Nelson–Aalen Plot with R
Justification for the Nelson–Aalen Estimate
Uncertainty of the Nelson–Aalen Estimator
14.7 Total‐Time‐on‐Test Plotting
14.7.1 Total‐Time‐on‐Test Plot for Complete Datasets
The Total‐Time‐on‐Test Transform
Example 14.14 (Exponential distribution)
Example 14.15 (Weibull distribution)
Three Useful Results
Example 14.16 (Ball bearing failures)
TTT Plotting with R
Example 14.17 (Age replacement)
14.7.2 Total‐Time‐on‐Test Plot for Censored Datasets
14.7.3 A Brief Comparison
14.8 Survival Analysis with Covariates
14.8.1 Proportional Hazards Model
Hazard Ratio
Cumulative Failure Rate
Survivor Function
Example 14.18 (Exponential distribution)
Example 14.19 (The MIL‐HDBK‐217 prediction method)
14.8.2 Cox Models
14.8.3 Estimating the Parameters of the Cox Model
Cox Model Analysis with R
14.9 Problems
References
Notes
15 Bayesian Reliability Analysis. 15.1 Introduction
15.1.1 Three Interpretations of Probability
Classical Probability
Frequentist Probability
Subjective Probability
Relevance for Reliability
15.1.2 Bayes' Formula
15.2 Bayesian Data Analysis
15.2.1 Frequentist Data Analysis
15.2.2 Bayesian Data Analysis
15.2.3 Model for Observed Data
15.2.4 Prior Distribution
Definition 15.1 (Prior distribution)
Remark 15.1 (Categories of Bayesians)
15.2.5 Observed Data
15.2.6 Likelihood Function
Example 15.1 (Likelihood function for binomial model)
15.2.7 Posterior Distribution
Definition 15.2 (Posterior distribution)
Example 15.2 (Discrete distribution)
Example 15.3 (Continuous distribution)
15.3 Selection of Prior Distribution
15.3.1 Binomial Model
Beta Prior Distribution
Posterior Distribution
Remark 15.2 (Conjugate distributions)
15.3.2 Exponential Model – Single Observation
Gamma Prior Distribution
Posterior Distribution
15.3.3 Exponential Model – Multiple Observations
Example 15.4 (Sequential updating)
15.3.4 Homogeneous Poisson Process
Example 15.5 (Marginal distribution of )
15.3.5 Noninformative Prior Distributions
Example 15.6 (Binomial model)
Example 15.7 (Exponential model)
15.4 Bayesian Estimation
15.4.1 Bayesian Point Estimation
15.4.2 Credible Intervals
15.5 Predictive Distribution
Example 15.8 (Exponential distribution)
15.6 Models with Multiple Parameters
15.7 Bayesian Analysis with R
15.8 Problems
References
Note
16 Reliability Data: Sources and Quality. 16.1 Introduction
16.1.1 Categories of Input Data
Sources of Reliability Data
16.1.2 Parameters Estimates
Failure Rates
CCF Estimates
Mean Downtime
Proof Test Interval and Coverage
16.2 Generic Reliability Databases
16.2.1 OREDA
16.2.2 PDS Data Handbook
16.2.3 PERD
16.2.4 SERH
16.2.5 NPRD, EPRD, and FMD
NPRD
EPRD
FMD
Automated Databook
16.2.6 GADS
16.2.7 GIDEP
16.2.8 FMEDA Approach
16.2.9 Failure Event Databases
16.3 Reliability Prediction
16.3.1 MIL‐HDBK‐217 Approach
Parts Stress
Parts Count
16.3.2 Similar Methods
16.4 Common Cause Failure Data
16.4.1 ICDE
NRC CCF Insights
16.4.2 IEC 61508 Method
16.5 Data Analysis and Data Quality
16.5.1 Outdated Technology
16.5.2 Inventory Data
16.5.3 Constant Failure Rates
16.5.4 Multiple Samples
16.5.5 Data From Manufacturers
16.5.6 Questioning the Data Quality
16.6 Data Dossier
16.6.1 Final Remarks
References
Note
Appendix A Acronyms
Appendix B Laplace Transforms
Theorem B.1
Example B.1
B.1 Important Properties of Laplace Transforms
B.2 Laplace Transforms of Some Selected Functions
Note
Author Index
Subject Index
Wiley Series in Probability and Statistics
Notes
WILEY END USER LICENSE AGREEMENT
Отрывок из книги
Established by WALTER A. SHEWHART and SAMUEL S. WILKS
David J. Balding, Noel A.C. Cressie, Garrett M. Fitzmaurice, Harvey Goldstein, Geert Molenberghs, David W. Scott, Adrian F.M. Smith, and Ruey S. Tsay
.....
and the survivor probability of the item may be defined as
The physical approach is mainly used for reliability analyses of structural elements, such as beams and bridges. The approach is therefore often called structural reliability analysis (Melchers 1999). A structural element, such as a leg on an offshore platform, may be exposed to loads from waves, current, and wind. The loads may come from different directions, and the load must therefore be modeled as a vector . In the same way, the strength will also depend on the direction and has to be modeled as a vector . The models and the analysis therefore become complicated. The physical approach is not pursued further in this book.
.....